
Key 4140 Material Properties Explained
Table of Contents
Introduction
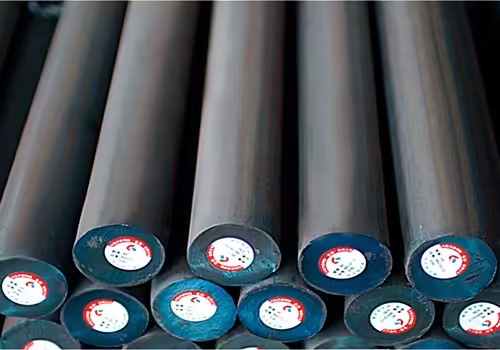
The 4140 alloy steel is a versatile and widely used material in industrial applications. Known for its excellent strength, toughness, and fatigue resistance, 4140 steel is a chromium-molybdenum alloy that serves in sectors such as automotive, aerospace, oil and gas, and machinery manufacturing. Understanding the core 4140 material properties is essential for selecting the right steel for your specific project or engineering needs.
In this article, we will delve into the essential characteristics of 4140 steel, exploring its chemical composition, mechanical behavior, heat treatment response, and real-world applications. Whether you’re a materials engineer, machinist, or buyer, this comprehensive guide will help you grasp the most critical 4140 material properties for informed decision-making.
Chemical Composition of 4140 Steel
One of the fundamental aspects of understanding 4140 material properties is its chemical composition. The specific blend of elements in 4140 steel is what gives it the unique combination of strength, toughness, and wear resistance that makes it ideal for demanding engineering applications.
Primary Composition Breakdown
- Carbon (C): 0.38–0.43%
Carbon is a critical element in steel alloys. In 4140 steel, it provides the foundation for strength and hardness. This relatively high carbon content allows the steel to be heat-treated effectively, improving its wear resistance and tensile strength without making it too brittle. - Chromium (Cr): 0.80–1.10%
Chromium adds to the steel’s hardness, tensile strength, and corrosion resistance. While 4140 is not stainless steel, the chromium content enhances its durability in moderately corrosive environments and helps in the formation of hard carbides, which contribute to wear resistance. - Manganese (Mn): 0.75–1.00%
Manganese increases hardenability and tensile strength. It also improves machinability and acts as a deoxidizer during steel production. The manganese content in 4140 ensures uniform hardness throughout the cross-section after heat treatment. - Molybdenum (Mo): 0.15–0.25%
Molybdenum helps improve the steel’s strength at high temperatures and enhances its resistance to softening during tempering. It also works synergistically with chromium to increase hardenability and reduce the risk of brittleness. - Silicon (Si): 0.15–0.30%
Silicon acts primarily as a deoxidizer, preventing the formation of gas bubbles in the steel during manufacturing. It also contributes slightly to strength and hardness. - Iron (Fe): Balance
Iron is the base metal in all steels. In 4140, it makes up the majority of the composition, binding all the alloying elements together and forming the steel’s fundamental matrix.
Why This Composition Matters
This specific combination of alloying elements results in a material that can be heat-treated to achieve a broad range of mechanical properties. For example, by adjusting the tempering process, manufacturers can tailor 4140 steel to be either more ductile or harder and more wear-resistant, depending on the intended application.
Furthermore, the presence of both chromium and molybdenum makes 4140 a chromium-molybdenum alloy steel, commonly referred to as “chromoly” steel. This classification underscores its superior performance in high-stress environments, such as those found in aerospace components, automotive parts, and oil and gas equipment.
Mechanical 4140 Material Properties
Mechanical performance is where 4140 steel truly excels. It combines high tensile strength with toughness and wear resistance, making it ideal for demanding applications.
Table: Mechanical Properties of 4140 Steel
Property | Annealed Condition | Hardened & Tempered Condition |
---|---|---|
Tensile Strength (MPa) | 655 | 850–1000 |
Yield Strength (MPa) | 415 | 700–850 |
Elongation (%) | 25 | 15–18 |
Hardness (Brinell) | 197 | 217–248 |
Impact Toughness (J) | High | Medium-High |
Modulus of Elasticity (GPa) | 205 | 205 |
These numbers provide a good starting point for engineers and designers evaluating 4140 material properties for structural or performance-based uses.
Heat Treatment and Its Impact on 4140 Material Properties
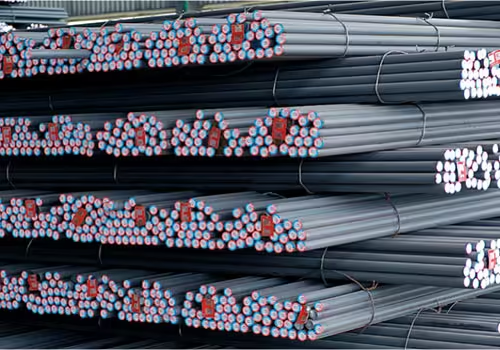
Among alloy steels, 4140 is particularly renowned for its exceptional response to heat treatment. This responsiveness is a defining factor in many of the enhanced 4140 material properties seen in high-performance applications. Through controlled heating and cooling cycles, the material’s hardness, toughness, and tensile strength can be significantly altered to meet diverse engineering requirements.
Heat Treatment Processes:
Each heat treatment method brings out different mechanical characteristics in 4140 steel:
- Annealing
This process involves heating the steel to around 845°C (1550°F) followed by slow furnace cooling. The result is a soft, ductile microstructure that makes machining easier. Annealed 4140 exhibits improved workability and reduced internal stresses, making it suitable for further forming or shaping. - Normalizing
In this process, 4140 steel is heated slightly above its critical temperature (approximately 870°C / 1600°F) and air-cooled. Normalizing refines the grain structure, which improves the material’s impact strength and toughness. It’s often used prior to final hardening treatments to ensure uniform mechanical behavior. - Quenching and Tempering
This two-step process is widely used to enhance hardness and tensile strength. After quenching in oil or water, the steel becomes extremely hard but brittle. Tempering at temperatures between 200°C and 650°C (400°F–1200°F) reduces brittleness and brings the material to a desired balance of toughness and strength. This method is ideal for manufacturing parts like high-load gears, drive shafts, and forged components.
The impact of these treatments on 4140 material properties is substantial. Post-treatment, the steel exhibits improved fatigue resistance, enhanced dimensional stability, and increased strength-to-weight ratios, making it suitable for demanding environments such as aerospace assemblies or oilfield equipment.
Applications Driven by 4140 Material Properties
The high versatility of 4140 steel lies in its ability to combine several key properties: high tensile strength, fatigue resistance, and good machinability. These characteristics enable 4140 to fulfill critical roles across industries where performance under stress is non-negotiable.
Common Industrial Applications
- Automotive
Components like crankshafts, axles, and connecting rods benefit from the combination of toughness and wear resistance. These parts often experience dynamic loads and require materials with superior fatigue strength. - Oil and Gas Sector
4140 is a staple for drill collars, mud motor shafts, and tool joints. In these applications, it provides the robustness needed to withstand high torsional loads, abrasiveness, and cyclic stress in harsh environments. - Aerospace
While not as commonly used as titanium or aluminum alloys, 4140 finds use in secondary structures such as wing spars, actuator parts, and landing gear supports due to its strength and cost-effectiveness. - Heavy Equipment and Industrial Machinery
Shafts, spindles, gears, and bolts made from 4140 steel are capable of bearing heavy loads without deformation or failure. Its adaptability to different surface treatments further enhances corrosion and wear performance.
These wide-ranging applications are all driven by the underlying 4140 material properties, particularly its balance of formability and mechanical resilience.
Typical Mechanical Properties of 4140 Steel (Quenched and Tempered)
Here is a summary table illustrating the key mechanical properties of 4140 steel after heat treatment:
Property | Value (Typical) | Notes |
---|---|---|
Tensile Strength | 655–1790 MPa | Varies with tempering temperature |
Yield Strength | 415–1650 MPa | Directly impacted by quenching and tempering process |
Elongation at Break | 10–25% | Higher with lower strength tempers |
Hardness (HRC) | 24–54 HRC | Can be controlled via tempering |
Impact Toughness | Excellent | Retained even in thicker cross-sections |
Machinability Rating | ~66% of B1112 | Annealed condition is easiest to machine |
These values may shift depending on specific production conditions, size of the part, and the thermal profile applied. However, they provide a general framework of what to expect from components engineered from this alloy.
Machinability and Welding Considerations
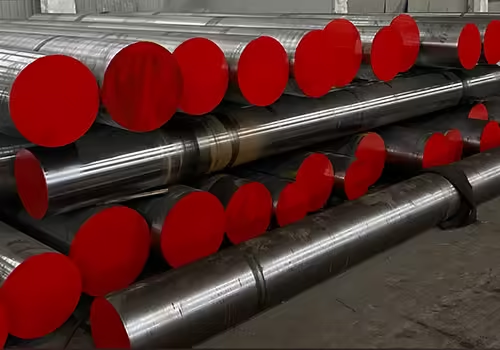
The machinability of 4140 is generally favorable, especially in its annealed state. With a machinability rating of around 66% (relative to B1112 steel at 100%), 4140 allows for precise fabrication of complex parts when using the right tools and techniques.
As the steel is hardened through quenching and tempering, machining becomes more challenging. High-speed tools with appropriate coatings (such as TiN or TiCN) are recommended, and coolant application is vital to minimize thermal distortion and tool wear.
Welding Requirements
Welding 4140 steel is possible but requires caution:
- Preheating is essential—typically to 150–300°C—to avoid cold cracking due to the high carbon and alloy content.
- Post-weld heat treatment (stress relief) between 550–650°C is often needed to restore ductility and minimize residual stresses.
- Low hydrogen welding processes (like GTAW or SMAW with low-hydrogen electrodes) are strongly recommended.
Proper technique preserves the integrity of the base material and ensures that the 4140 material properties are not compromised in the heat-affected zone.
Best Practices for Working with 4140 Steel
- Use carbide or cobalt high-speed cutting tools for machining
- Maintain consistent coolant flow to manage thermal buildup
- Always preheat before welding, and apply post-weld stress relief
- Avoid rapid cooling after welding to reduce the risk of cracks
- Conduct hardness tests after heat treatment to confirm results
These guidelines help maintain the material’s reliability across its lifecycle—from manufacturing to deployment in the field.
Conclusion
Choosing the right steel for your application means balancing strength, ductility, hardness, and machinability. 4140 steel strikes that balance exceptionally well, offering a suite of performance benefits driven by its alloying elements and response to heat treatment.
From automotive parts to oilfield components, 4140 material properties provide a reliable solution for high-stress environments. Understanding these properties allows engineers and manufacturers to achieve efficiency, safety, and performance goals.
FAQ
What makes 4140 steel different from other alloy steels?
4140 steel is distinguished by its unique combination of chromium and molybdenum, elements that contribute significantly to its enhanced mechanical characteristics. These alloying elements improve its tensile strength, fatigue resistance, and toughness, making it more robust than many standard carbon steels. One of the most notable 4140 Material Properties is its excellent hardenability, which allows it to be heat treated for a wide range of industrial applications. This versatility makes it a preferred choice for components that must endure high stress and wear.
Can 4140 steel be welded?
Yes, 4140 steel is weldable, but it demands careful preparation. Due to its high hardenability—one of the critical 4140 Material Properties—the steel is prone to cracking if welded without precautions. To ensure a successful weld, it is essential to preheat the material, typically to 300–400°F (150–200°C), and to apply post-weld heat treatment to relieve residual stress. These steps help maintain the structural integrity and mechanical performance of the final component.
Is 4140 steel corrosion-resistant?
While 4140 steel does exhibit slightly better corrosion resistance than plain carbon steels due to its chromium content, it is not considered a stainless alloy. Therefore, it can rust or corrode over time if exposed to moisture or harsh environments without protective coatings. Among the commonly referenced 4140 Material Properties, corrosion resistance is not its strongest suit. For applications in corrosive environments, additional surface treatments such as plating, painting, or the application of corrosion inhibitors are recommended.
How hard can 4140 steel get?
One of the standout 4140 Material Properties is its ability to reach high hardness levels after heat treatment. When quenched and tempered properly, 4140 steel can achieve hardness ratings up to approximately 50 HRC (Rockwell Hardness). The exact hardness depends on the specific heat treatment cycle, including quenching medium, tempering temperature, and hold time. This makes the steel especially useful for parts like gears, axles, and dies that require both wear resistance and toughness.
Where is 4140 steel commonly used?
Thanks to its outstanding mechanical characteristics, 4140 steel finds widespread use across multiple high-demand industries. Common applications include drive shafts, crankshafts, spindles, bolts, gears, and machine tool components. The automotive, aerospace, oil and gas, and manufacturing sectors all rely heavily on 4140 Material Properties to ensure strength, fatigue resistance, and long service life in demanding environments. Its adaptability to both machining and heat treatment further enhances its role in critical engineering designs.