
8 Powerful Trends Shaping Steel Grades in 2025
In 2025 the global steel industry is being reshaped by sweeping technological, regulatory, and market forces. Buyers must now consider more than just basic yield strength or price when choosing a steel grade – they must weigh new advanced alloys for lightweighting, the carbon footprint of steelmaking, digital traceability of products, and compliance with evolving global specifications. Steel producers and users are embracing sustainability goals, AI-driven production, and smart manufacturing, all of which have profound implications for material selection.
For example, automakers are increasingly using ultra-high-strength steels (UHSS) instead of heavier materials to reduce vehicle mass while meeting crash standards. At the same time, “green steel” (produced via hydrogen reduction or recycled scrap) is emerging to satisfy net-zero mandates. To succeed, procurement teams must stay informed about these trends and how they affect specifications across ASTM (US), EN (EU), JIS (Japan) and other standards. The following sections examine eight key trends in detail, providing buyers with the insight needed to specify the right steel grades for 2025 and beyond.
Figure: A modern steelmaking facility combines robotics, AI monitoring, and connected workflows – illustrating how Industry 4.0 and automation are transforming steel production and the properties of steel available to buyers
Table of Contents
1. Innovative High-Strength, Lightweight Alloys
Lightweighting and strength continue to drive steel innovation. Automakers, aerospace designers, and construction engineers all demand steels with higher yield and tensile strengths so structures can be lighter without compromising safety. Advanced High-Strength Steels (AHSS) are a major focus: first and second-generation AHSS (dual-phase, TRIP, TWIP steels, etc.) already enable thinner sections with strengths around 500–1000 MPa. Now third-generation AHSS grades target both very high strength and good formability, often using complex multi-phase microstructures.
For example, experimental 3rd-gen steels have exceeded 1500 MPa tensile strength while still allowing 20–25% elongation. In a recent electrified vehicle project, design teams used “a significant proportion of >1500 MPa grades, primarily for occupant and battery intrusion zones”. Press-hardened (boron-alloyed) steels like 22MnB5 (roughly EN 10149-2 or ASTM A1008 if hot-formed) are common in ultra-high-strength applications. Buyers will see more of these specialty grades – often specified by strength (e.g. “YS 1500 MPa steel”) or proprietary names – rather than just general labels like “mild steel.”
At the same time, lower-carbon alloys with higher strength are replacing traditional mild steels. For example, HSLA structural steels (such as ASTM A572 Grade 50 or EN S355) offer about 355 MPa yield – versus ~250 MPa for basic grades like ASTM A36 or EN S275 – while remaining weldable. These allow lighter sections in buildings and bridges. Niche ultra-strong steels (compositions including Cr–Mo, Ni, or Mn) meet aerospace and defense needs. One automotive steel alliance notes that evolving AHSS are “becoming increasingly stronger at thinner gauges and formable for complex shapes”, enabling weight savings in vehicle bodies.
Implications for buyers: When ordering steels for 2025 projects, expect requests for higher minimum strengths and possibly new chemistries. Engineers may specify dual-phase or trip steels by their trade names or composition, and press-hardenable grades by hardening treatment. In structural and machinery specs, HSLA steels are often indicated by codes like ASTM A992 or EN S460 (yield 460 MPa) for high-yield needs. Buyers should compare equivalent standards carefully (e.g. ASTM vs EN vs JIS), since naming conventions differ internationally.
They must also confirm that higher-strength steels meet formability or welding requirements (some new grades are less ductile or require special processing). Global projects will need cross-reference charts: for instance, ASTM A36 (~250 MPa yield) is roughly equivalent to EN S275JR or JIS SS400, and A572 Gr 50 (~345 MPa yield) to EN S355JR. Savvy procurement teams will note that EN and JIS often express strength in MPa and use “S” or “SS” codes (e.g. S355JR, SS400) while ASTM/SAE use alphanumeric grade numbers. Keeping a multi-standard conversion guide on hand helps ensure the right grade is supplied from any source.
2. Green Steel and Decarbonization Efforts
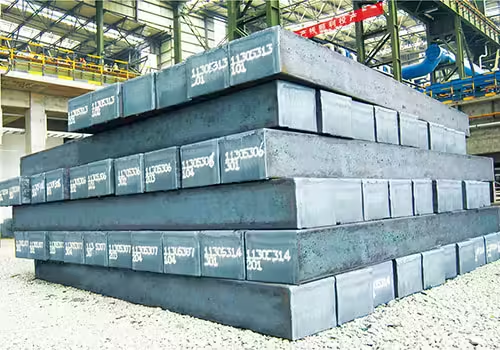
Sustainability is no longer a niche concern – it’s now a major driver of steel specification. Regulators, investors, and customers demand steel with a lower carbon footprint. “Green steel” technologies – such as hydrogen-based direct-reduced iron (DRI) plants, electric-arc furnaces powered by renewables, and advanced carbon capture – are being rapidly adopted by leading producers. In Spain, for example, ArcelorMittal will have its Sestao plant produce zero-emissions steel by 2025 by switching to green hydrogen DRI and increasing scrap usage in EAF furnaces.
Electric Arc Furnaces (EAFs), which can run on recycled scrap and clean electricity, are growing in share (EAFs produced ~41% of steel in 2024). Policy measures reinforce this shift: the EU’s Carbon Border Adjustment Mechanism (CBAM) and waste-export regulations effectively force European steelmakers and buyers to decarbonize or pay penalties.
Figure: Infographic highlighting the rise of hydrogen DRI, EAF scrap smelting, and recycled steel in achieving “green steel.” Buyers face new certification regimes (carbon footprint labels, digital product passports) to verify claims.
New carbon accounting standards and certifications are emerging for steel. Buyers may now see requirements like “x kg CO₂/ton maximum” or certifications from schemes such as Responsible Steel or ISO 14064 carbon inventories. One industry report notes that “green steel promises a lower-emission alternative, but its premium has tracked at 20–40%” of price. In response, major users of steel are forming long-term sourcing partnerships and pressing for verified sustainability data. The EU’s Digital Product Passport rules will also mandate traceable lifecycle information (including carbon data) for steel products by 2026.
Implications for buyers: Expect to see sustainability clauses in steel contracts. Buyers may be asked to preferentially select steel mills or grades produced by EAF or hydrogen DRI routes. Specifications could require a certain percentage of recycled content or a certified “low-carbon” label. Tracking and documentation will be crucial: digital systems may be used to trace each steel coil’s energy mix and scrap ratio.
Buyers should clarify how any added costs (green premiums) align with their customers’ eco-standards. In some cases, regions will phase in only low-carbon steels (as in parts of Northern Europe), affecting imports. Overall, procurement teams will need to balance traditional grade properties with these new environmental attributes, essentially treating carbon footprint as a spec parameter alongside tensile strength or composition.
3. Digitalization and Material Traceability

The steel supply chain is undergoing a digital transformation that affects grade certification and provenance. Regulators (especially in the EU) and large industrial buyers are demanding full chain-of-custody transparency. A prime example is the EU’s Digital Product Passport (DPP) initiative: by 2025, all “iron, steel, and aluminum products” sold in Europe must carry a digital passport containing detailed material data. In practice, this means every steel plate or bar will have a unique identifier (via QR code or RFID) linking to a cloud database showing its origin, chemistry, processing history, and recycling data. Products with high environmental impact (including structural steel in buildings) are targeted first.
Industry is already prototyping such systems. For example, Tata Steel UK partnered with a blockchain startup to create a “digital passport” for each steel product. Now a buyer can scan the material with a smartphone and instantly retrieve its grade, mill test certificate, and even a calculated carbon footprint. This technology is being seen as essential for “responsibly sourced materials” – enabling buyers to verify that the supplied steel truly meets the specified alloy and decarbonization claims. In the future, such traceability may extend across borders: global standards like ISO 15459 (UIDs) will ensure codes match worldwide.
Implications for buyers: Steel grades will increasingly be tied to digital certificates. Rather than rely on paper test reports alone, purchasers may be expected to accept or mandate digital records (often standardized by ISO or ASTM Document standards). This affects specifications in two ways. First, buyers can demand exact verification of composition and heat-treatment for every batch of steel. A lot of uncertainty is removed: defects or mismatches can be traced back to the mill. Second, sustainability targets can be met with verifiable data – for example, requiring an X% recycled content or a lower carbon footprint grade.
Importantly, international shipments will need matching standard references: a grade specified under ASTM may need the buyer to check the EN or JIS equivalent to ensure the digital passport covers the right alloy composition. In short, the old mill test certificate is evolving into a global digital asset, and procurement systems must adapt to retrieve and store this information for compliance and auditing.
4. Global Standards and Specification Convergence
Steel is sold on every continent, but each region has its own standards. Navigating ASTM (US/ANSI), EN (Europe), JIS (Japan), and other national codes is an ongoing challenge for global buyers. In practice, many project specifications now list equivalent grades across systems. For example, a structural specification might accept “ASTM A36 (S275JR/JIS SS400) or equivalent,” and a stainless order might allow “304/304L (EN 1.4301) or 316 (EN 1.4401).” Grade equivalence charts (like those published by industry associations) are frequently used to cross-map yield/tensile properties and chemistry.
Nevertheless, differences remain. A single grade name does not always mean identical chemistry or tolerances. For instance, “A36” (US) and “S275JR” (EN) both target ~250 MPa yield, but their manganese and carbon limits differ slightly. Australian (AS), Chinese (GB), and other systems add more complexity. In some cases, buyers might switch between naming conventions: a material ordered as ASTM A992 (a popular U.S. high-strength structural steel) might have to be matched to EN S355J2 in Europe. There are also new ISO standards emerging that aim to harmonize steel grade classification, but complete unification is elusive.
Implications for buyers: Clarity in specifications is paramount. When drafting purchase orders, include a table or reference specifying all acceptable equivalents (e.g. “Grade 304/EN 1.4301” for stainless). Demand mill certificates that cite the exact standard. Be aware that some modern grades have no direct one-to-one match: third-generation AHSS, for example, are often proprietary and may not appear in common standards. In practice, buyers often rely on material producers or testing labs to confirm equivalence. As demand for traceability grows (see Trend 3), mills may increasingly list multiple standard designations on a single certificate.
In any case, procurement should work closely with engineers to ensure that a steel with different designation still meets all needed ASTM/EN/JIS criteria (tensile, toughness, chemistry) for the application.
5. Electrification and Automotive Demand
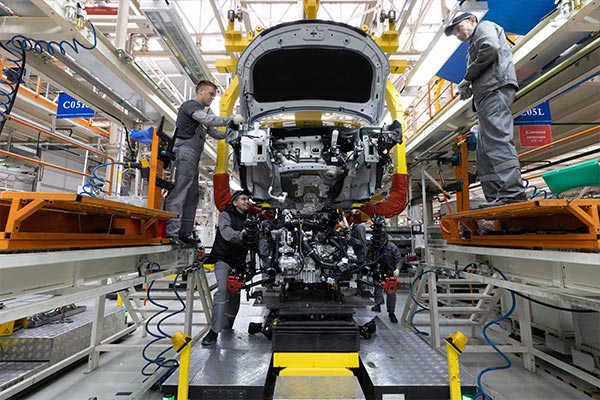
The rapid growth of electric vehicles (EVs) and related technologies is reshaping steel demand. Auto manufacturers still use vast amounts of steel – often more per vehicle in heavy-duty EVs – but the mix of grades is changing. Battery electric cars require larger, more rigid frames to protect heavy battery packs, driving the use of ultra-high-strength steels in crash zones (often 1,000–1,500 MPa minimum yield) along with extensive use of formed, spot-welded components. The “body-in-white” designs of many new EV platforms feature more dual-phase and press-hardened steel sections than older platforms.
Another impact is in electrical steel for motors and transformers. EV powertrains depend heavily on non-grain-oriented electrical steel (NGOES) for motors, which must have very high magnetic permeability and low core loss. In fact, the NGOES segment accounted for over 71% of the U.S. electrical steel market in 2024, with EV motors as the dominant driver. Grain-oriented electrical steel (GOES), used in transformers and generators, is also being pushed by renewable integration. Large steel producers are investing heavily here: for example, ArcelorMittal invested $1.2 billion in 2025 to expand NGOES production at a new mill for EV and energy applications.
Meanwhile, the overall pace of global steel demand has shifted; automotive’s share of steel use is rising as many power-producing (blast furnace) industries plateau. Governments’ clean-vehicle incentives and stricter fuel economy standards mean automakers cannot easily substitute steel with aluminum or composites for large structural parts. Consequently, steel remains integral but is used more efficiently. In oil & gas and mining equipment, similar electrification (e.g. hydrogen-powered drills) tends to favor steel for high-temperature and wear-resistant grades, rather than archaic materials.
Implications for buyers: Steel requests tied to EV projects will emphasize different properties. A supplier might be asked for high-strength low alloy (HSLA) steels in car chassis and for high-quality NGO electrical steels in motors. Buyers should ensure motor core laminations meet Class 35XX or 45XX electrical steel specs (often ordered by thickness and silicon content). For structural components, be prepared to source steels like ASTM A153 (galvanized rebar) if building charging stations, or higher-end alloys if making EV supporting infrastructure.
Additionally, because EVs often emphasize sustainability, steel supplied for EV manufacturing is likely to come under stricter traceability and recycled-content scrutiny (per Trends 2–3). Finally, with EV battery standards requiring fire resistance, buyers may see more queries for phosphorus-alloyed steels or flame retardant coatings – a niche but emerging concern.
6. Modular Construction and Infrastructure Growth
Construction is embracing prefabrication and high-performance materials. Modular building methods – where whole sections of building are fabricated off-site in steel – are gaining momentum globally. This trend is driven by efficiency (speed of assembly), safety, and sustainability (factory conditions enable better quality control). As one industry report notes, modular construction is focusing “on lightweight steel, high-strength alloys, and advanced manufacturing techniques (like 3D printing) for faster, more efficient construction”. Similarly, stringent building codes and green building standards are pushing innovation “towards sustainable and eco-friendly steel materials”.
In practical terms, buyers will encounter more specifications for high-yield structural steels in buildings. For high-rise or seismic-prone structures, grades like EN S460NL or ASTM A572 Gr 65 (460–450 MPa yield) allow slimmer columns and beams. Demands for corrosion resistance also grow: weathering steel (like ASTM A242 “Corten” or EN 10155 weathering grades) is often required for exposed facades and bridges because it forms a stable rust patina.
For instance, the ASTM A242 spec was created for structural sections “where weight savings and atmospheric corrosion resistance are important”. Stainless steel or duplex grades (UNS S31803) are increasingly used in coastal infrastructure to withstand salt air, and galvanized steels are specified more rigorously (e.g. thicker zinc coatings per ASTM A123 or hot-dip standards).
Figure: Wind turbine towers and prefabricated steel beams under construction. The infrastructure boom (wind farms, transit projects, etc.) is increasing demand for high-yield, weathering, and specialized structural steels (for example EN S355J2+N or ASTM A709 Grade 50W).
Large-scale infrastructure funds (e.g. U.S. Infrastructure Act, EU Green Deal) are translating to more steel use in bridges, rails, and energy. High-strength, weldable bridge steels like A709 Gr 50 (US) or EN S460 are common. Steel used in pipelines and pressure vessels (ASTM A106, EN P265GH) are in demand for gas and water projects. Meanwhile, higher lifetimes are expected, so corrosive-service grades (e.g. Chrome-Moly grades such as ASTM A335 P91) see more use in power plants and petrochemical plants.
Implications for buyers: Steel orders for construction projects will emphasize grade codes and material forms. Buyers should clarify weathering vs. painted steel, specify yield if needed, and confirm impact toughness requirements (particularly for cold environments). Prefabricated modules often require tight tolerances (narrower coils, precision cutting), so processed steels (CAM-certified) may be needed.
As codes evolve (like ISO 1993 updates or national annexes), certain grades may become mandatory (for example, EN S890 becomes a “locked” grade for wind tower steel). Buyers sourcing internationally should double-check that imported structural steels meet local code designations. In summary, the construction trend means procurement must be able to provide everything from A36/S235 for non-structural parts up to specialized ASTM A588 (weathering) or EUW (thermo-mechanically rolled) structural grades for high-stress uses.
7. Circular Economy and Recycling
Steel is inherently recyclable, and 2025 will see further emphasis on the circular economy. More than 460 million metric tons of steel scrap were melted globally in 2024 – already the largest-tonnage recycled material on earth. However, that number plateaued recently as direct-reduced iron (DRI) growth (for green steel) competed with scrap in furnaces. Still, new policies are tilting the balance toward scrap. For example, the EU’s Waste Shipment Regulation (WSR) now restricts exports of scrap to non-OECD countries, meaning European steelmakers must find enough quality domestic scrap or import it from OECD partners. This feeds into decarbonization goals but tightens scrap availability.
In parallel, material science innovation is producing second-generation steel recycling. New processes capture more alloying elements or allow alloy diversification in scrap, maintaining quality. Some manufacturers advertise steels with a percentage of “post-consumer recycled content,” similar to reclaimed aluminum standards. At procurement level, this trend means that “recycled content” may enter purchase specs or claims. Industry surveys show that with over 90% of steel production in decarbonizing countries, the demand for low-carbon (i.e. high-recycled) steel is “at an all-time high”. Recyclers argue they are key to the transition, but reliable data on scrap content must be demonstrated in reports.
Implications for buyers: Preparation is required for new scrap-related requirements. Some projects may literally specify a target scrap ratio (e.g. steel made with ≥30% post-consumer scrap). Certifications or chain-of-custody documentation (overlapping Trend 3) will back these claims. Pay attention to grade availability: certain high-alloy steels (like tool steel or spring steel) are less recyclable, so alternatives or concessions may be needed. From a practical standpoint, buyers should consider inventory strategies: increased recycling emphasis can lead to volatility in long-lead-time alloy availability. Additionally, recycled-content steel may differ slightly in trace elements; requiring bright-bars vs hot-rolled, or tighter chemistry checks in ordering, could become common.
8. Smart Manufacturing and 3D-Printed Steel
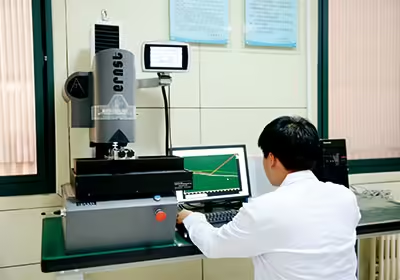
Industry 4.0 is permeating steel as well. Advanced factories use AI and IoT to optimize everything from melt chemistry to delivery schedules. For buyers, this translates into ever-more-precise control of steel properties. On the production side, AI-driven quality control yields more consistent grades (fewer off-spec heats). Predictive maintenance and digital twin simulations allow mills to run processes closer to ideal, reducing scrap. Such capabilities are discussed in industry trend reports: for example, AI and ML are “revolutionizing steel fabrication,” enabling real-time process optimization and waste reduction.
Figure: A demonstration of “smart steel” manufacturing and metal additive printing. Smart factories, embedded sensors, and metal 3D printing are enabling new steel component types – from complex aerospace brackets to on-site construction parts – altering how grades are specified in design.
Meanwhile, additive manufacturing (3D printing) of steel is moving from labs into niche production. Companies are now printing structural steel components (using processes like DED or powder-bed) for aerospace, tooling, and even construction. The printed steels are often special alloys (stainless, maraging, or novel high-strength mixes) and come with unique certification: each build requires a full material cert because the microstructure can differ from wrought steel. This means buyers sourcing 3D-printed parts must handle new material specs (often referring to standards like ASTM F3184 for printed maraging steel, or SAE AMS for printed 316L).
Embedded sensors and “smart” steel parts are also emerging: some structural members now incorporate fiber optics or electronics during manufacture for real-time health monitoring. Nano-structured steels (with engineered grain sizes or precipitates) are likewise being commercialized for specialized applications.
Implications for buyers: Specifications may start to include additive options or data-rich deliverables. For instance, a contract might allow a 3D-printed valve body if it meets ASTM performance tests (tensile, hardness, porosity). Procurement will need to ensure that any new manufacturing method (like laser powder-bed) has its own process qualification and traceability. Also, as factories automate, lead times may shrink but minimum order quantities or production lots might change. Buyers should watch for opportunities – e.g. small, custom batches of complex shapes – but also be ready to define “equivalent properties” between printed and traditional steels.
At the very least, expect stronger communication from mills about how their smart-manufacturing yields more uniform chemistry and properties (for example, AI control may guarantee ±2 MPa tighter tensile ranges than older methods).
Comparative Table: Common Steel Grades in 2025
Grade (Standard) | Type/Category | Typical Strength (MPa) | Common Uses | Corrosion Resistance | Heat-Treatable? |
---|---|---|---|---|---|
ASTM A36 (EN S275JR, JIS SS400) | Carbon Mild Steel | YS ~250; TS 400–550 | Structural beams, plates, general fabrication | Low (requires painting) | Yes (annealing/normalizing) |
ASTM A572 Grade 50 (EN S355) | HSLA Structural Steel | YS ~345; TS ~450–550 | Heavy beams, columns, bridges, machinery | Moderate (painted/Galv) | Yes (can normalize, some Q&T) |
AISI 4140 (EN 42CrMo4) | Alloy Steel (Cr-Mo) | YS ~415; TS ~655 | Shafts, gears, high-strength fasteners | Low (requires coating) | Yes (quenched + tempered) |
Stainless 304 (EN 1.4301) | Austenitic Stainless | YS ~215; TS 520–720 | Food equipment, architecture, chemical plants | Excellent (general use) | No (only anneal) |
Stainless 316 (EN 1.4401) | Austenitic Stainless | YS ~170; TS ~520–680 | Marine hardware, medical, chemical, high-temp use | Superior (chlorides) | No (only anneal) |
ASTM A242 (Corten) (EN S355W) | Weathering (HSLA) Steel | YS ~345; TS ~470–550 | Bridges, buildings, containers requiring patina | Good (exposed, forms patina) | No (designed to rust) |
Notes: Tensile (TS) and Yield (YS) strengths are approximate. Corrosion resistance is relative: 304/316 SS are excellent versus general media, while Corten steels resist atmospheric rusting but must form a protective oxide layer. Heat treatment (“HT”) compatibility: Plain carbon and HSLA grades can be normalized or quenched+tempered for higher strength, alloy steels (like 4140) require quenching and tempering, whereas austenitic stainless steels (304, 316) cannot be hardened by heat – they are work- or strain-hardenable only.
The table above illustrates how key grades differ. Buyers should note that EN and ASTM grades do not always align perfectly (e.g. ASTM A572 Gr 55 has higher nominal yield than EN S355J2). Always verify properties like impact toughness, especially for welded structures or low-temperature service.
Conclusion
In summary, 2025 will see steel grade choices driven by more factors than ever. Buyers must navigate a complex landscape: cutting-edge alloys and fabrication methods, strict sustainability mandates, and interconnected global standards. Understanding the latest in advanced high-strength steels, green production methods, digital traceability, and market-specific demands (EVs, construction, etc.) is essential. Each trend above – from innovative AHSS to digital product passports – translates into concrete requirements in purchase specs. Smart procurement means blending traditional criteria (strength, ductility, corrosion resistance) with new ones (carbon intensity, recycled content, trace data). By staying informed and working closely with suppliers and engineers, buyers can make confident decisions that meet performance goals and future-proof their projects against evolving regulations.
In practice, this means using multi-standard grade equivalence tools, requiring mill certificates to reference carbon emissions or recycling when needed, and choosing suppliers who adopt Industry 4.0 practices. It also means asking questions: e.g., “Can this structural steel be certified by ResponsibleSteel?” or “What is the carbon footprint of this batch?” The answers to these questions will help align projects with global sustainability targets while ensuring that the chosen steel grade truly fits the intended application.
FAQ
Q: What exactly is “green steel,” and how does it differ from traditional steel?
A: Green steel refers to steel produced with dramatically lower CO₂ emissions. This is achieved by using electric-arc furnaces (often powered by renewable electricity) and green hydrogen DRI instead of conventional coal-fired blast furnaces. The steel chemistry (grades) can be the same, but the production route cuts emissions. Buyers may see green steel sold at a premium, and will want certification of its low-carbon attributes.
Q: How are EVs affecting steel selection?
A: The growth of EVs is driving demand for very high-strength steels (for lighter, safer car bodies) and for specialized electrical steels. EV batteries require robust steel enclosures, so grades like DP800 or press-hardened steels (1300–1500 MPa) are used in battery racks. Electric motors require NGO electrical steel with specific magnetic properties. In sum, EV projects may call for new grades (e.g. motor core laminations) and may demand traceability of motor-grade steel.
Q: When should I specify a stainless vs. a carbon steel?
A: Use stainless steel (like 304 or 316) when corrosion resistance is critical (chemicals, food, outdoor salt exposure). Mild/structural carbon steels (like A36/S275 or A572/S355) are used for general structures and machinery. The table above can help: for example, 304 SS has “excellent” general corrosion resistance, whereas A36 has only “low” resistance (needs coating). Also consider heat treatment: if you need to harden the part, stainless (304/316) won’t respond – a carbon or alloy steel (4140, for instance) would be needed instead.
Q: How do I compare ASTM, EN, and JIS grades?
A: Each standard uses its own numbering and tests. A common approach is to use an equivalence chart. For example, ASTM A36 ≈ EN S275JR ≈ JIS SS400 (all ~250 MPa yield). There are online tools and published tables (see RelianceFoundry or ReidSupply) that list equivalents across systems. When ordering, specify all applicable standard designations, or agree on one and verify matching chemistry and property requirements via mill certificates. Remember: even “equivalent” grades can have slight differences, so always check the spec limits.
Q: What new steels should buyers be aware of in 2025?
A: Look out for the latest advanced high-strength steels (often marketed by tensile strength, e.g. “1200 MPa DP steel”), press-hardenable (bake-hardenable) steels for automotive, and electrical steel grades for EVs (these often start with “3” in EN notation, like 3%Si grade, or ASTM A677). Also, weather-resistant structural steels (with codes like “W” in ASTM or “W” suffix in EN) are increasingly used for outdoor structures. Finally, with additive manufacturing, powder metallurgy grades (like maraging or specialized 17-4PH analogues in 3D-printed form) are emergent. Buyers should ask suppliers about any new offerings, and insist on certifications and test data for unfamiliar materials.
Q: How will regulatory trends affect my steel purchase?
A: Regulations are tightening on emissions and sustainability. In practice, you may face:
- Carbon regulations: e.g. CBAM in the EU, requiring proof of CO₂ per ton.
- Digital product passports: requiring trace data for steel.
- Local content rules: incentives for using domestic or recycled material.
- Recycling targets: mandates for recycled content in construction materials.
These may appear as contract clauses. To meet them, buyers need documentation from mills (CO₂ certificates, scrap content) and possibly to select mills in compliant regions. Planning ahead (e.g. including extra lead time for documentation) will be important.
By considering these eight trends – and adjusting procurement strategies accordingly – steel buyers can stay ahead of the curve. The steel grades chosen today will set the stage for performance, cost, and compliance for years to come.