
7 Key 1020 Steel Properties You Must Know
Table of Contents
Introduction
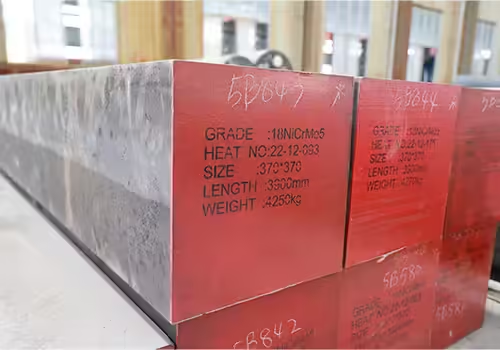
When choosing materials for engineering or industrial applications, understanding the mechanical and chemical characteristics of the steel you plan to use is critical. One of the most commonly utilized low-carbon steels in the market is 1020 steel. Known for its balance of strength, ductility, and affordability, this material has become a go-to choice for various industries ranging from automotive to construction.
This comprehensive guide will explore the most essential 1020 steel properties you need to know to make informed decisions for your projects. Whether you are an engineer, manufacturer, or student, understanding these properties will help you appreciate why 1020 steel is so widely adopted in today’s industrial world.
What Is 1020 Steel?
Before delving into the key 1020 steel properties, it’s important to understand what 1020 steel actually is. 1020 steel is a low-carbon steel alloy composed primarily of iron with a carbon content of around 0.18–0.23%. The “10” in the 1020 designation indicates a plain carbon steel, while the “20” denotes the carbon content.
Because of its low carbon content, 1020 steel is highly machinable and weldable. It’s often used in cold-drawn or hot-rolled form and can be carburized to enhance surface hardness while maintaining a soft core. This versatility makes it suitable for a wide variety of structural and mechanical applications.
Let’s now dive into the key 1020 steel properties that define this material’s behavior and performance.
Mechanical 1020 Steel Properties
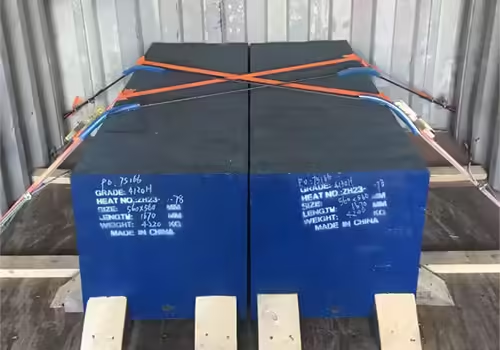
1. Tensile Strength and Yield Strength
One of the primary mechanical attributes that engineers and designers consider in steel is its strength profile. For 1020 steel, both the tensile strength and yield strength are within a range that supports structural integrity under moderate loads. These values form the core of 1020 steel properties when evaluating its use in real-world applications.
Tensile strength typically ranges between 394 MPa to 550 MPa, with variations depending on whether the steel has been cold-drawn or hot-rolled. Cold drawing increases strength slightly due to strain hardening, making the material more suitable for precision applications.
The yield strength averages around 295 MPa, meaning the material begins to plastically deform at this stress point. Beyond this limit, it won’t return to its original shape if the stress is removed.
This combination of tensile and yield strength makes 1020 steel a smart choice for manufacturing components like shafts, axles, connecting rods, and machine parts where moderate force is expected. These characteristics are key highlights when comparing various 1020 steel properties to alternative materials.
While not as strong as medium- or high-carbon steels like 1045 or 1060, it offers a good trade-off between strength and processability. The strength profile ensures that 1020 steel can withstand daily operational loads without premature failure or deformation, making it suitable for general-purpose applications in automotive, agriculture, and machinery.
2. Ductility and Elongation
Ductility is a measure of a material’s ability to deform under tensile stress. Among the notable 1020 steel properties, high ductility is a significant advantage. This is particularly beneficial in manufacturing settings that require shaping, bending, rolling, or drawing.
1020 steel typically exhibits 15–20% elongation over a 50 mm gauge length, which is a solid indicator of its stretchability without fracture. This property contributes significantly to the adaptability and usefulness of 1020 steel properties in metalworking industries.
Its low carbon content allows it to be cold-formed without cracking, making it ideal for parts that need to be molded or reshaped during fabrication.
Because of this high ductility, 1020 steel is often used in applications such as drawn tubes, bent brackets, rolled metal components, and cold-headed fasteners.
It also allows for better control during manufacturing processes like stamping, forging, or extrusion. This not only reduces the risk of part failure but also cuts down on waste and increases production efficiency.
In essence, this property allows manufacturers to create complex shapes while maintaining structural reliability. Even when the steel undergoes considerable deformation, it retains much of its internal cohesion and load-bearing capacity. Ductility is thus an essential part of the mechanical 1020 steel properties that manufacturers prioritize.
3. Hardness and Wear Resistance
Hardness in steels is directly related to their resistance to indentation, scratching, and general surface wear. In the case of 1020 steel, its baseline hardness is relatively moderate but can be improved with additional treatment methods. This aspect makes up another critical dimension in the range of 1020 steel properties.
Brinell hardness typically ranges from 119 to 143 HB in its normalized condition. This value indicates a surface that is soft enough for easy machining but strong enough to resist light surface damage.
As-is, the wear resistance of 1020 steel is considered adequate for moderate-duty applications. However, for higher performance, it is common to carburize the surface.
Carburization, a heat treatment process where the steel surface is enriched with carbon, can significantly enhance hardness and wear resistance. After this treatment, the outer layer can achieve hardness values upwards of 60 HRC, while the core retains its ductility.
This property combination is especially useful for components such as gear blanks, sprockets, bushings, camshafts, and mechanical pins.
The improved surface performance ensures that parts subjected to friction or contact fatigue last longer, reducing downtime and maintenance costs. However, it is important to note that without protective treatments or coatings, 1020 steel is not suitable for extremely abrasive environments.
For many design engineers and machinists, the hardness and wear resistance among 1020 steel properties represent a balance between manufacturability and longevity.
4. Fatigue Strength and Impact Resistance
In real-world applications, materials are often subjected not just to static loads, but to repeated cycles of stress. This is where fatigue strength comes into play. It measures how well a material can endure cyclic loading without crack initiation or propagation, and it’s an essential inclusion in 1020 steel properties.
1020 steel typically has a fatigue strength around 210 MPa, depending on surface finish and loading conditions. While not as high as alloy steels like 4140, it is adequate for many mechanical components in rotating machinery or moving assemblies.
The ability to absorb energy and withstand shock loading is another key factor. 1020 steel performs reliably in normal atmospheric and working temperatures, maintaining its integrity even when subject to sudden forces or impacts.
This resilience makes 1020 steel a reliable material for applications that involve rotational loading, shock-absorbing components, and vibration-dampening parts in equipment and vehicles.
It is also worth mentioning that the impact resistance of 1020 steel can decrease at extremely low temperatures, making it less ideal for cryogenic applications unless additional processing is used.
Chemical 1020 Steel Properties
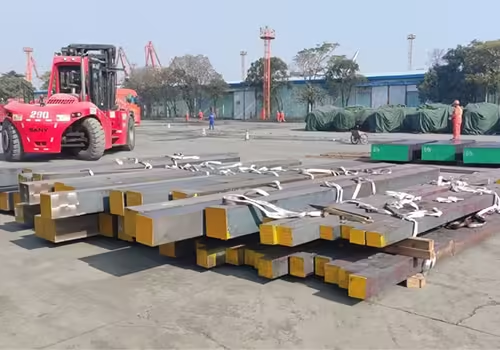
5. Composition and Corrosion Behavior
Understanding the chemical composition is vital when evaluating 1020 steel properties. Here’s a breakdown:
Element | Composition (%) |
---|---|
Carbon | 0.18–0.23 |
Manganese | 0.30–0.60 |
Phosphorus | ≤ 0.040 |
Sulfur | ≤ 0.050 |
Iron | Balance |
The low carbon content is responsible for its high machinability and weldability. Manganese improves strength and hardness while still retaining ductility.
However, 1020 steel is not inherently corrosion-resistant. It lacks sufficient chromium, nickel, or other corrosion-resistant elements found in stainless steel. Therefore, protective coatings like galvanization or painting are often applied when corrosion is a concern.
Thermal and Machinability Properties
6. Heat Treatment Behavior
One of the key reasons 1020 steel is popular in industry is its response to heat treatment. While it cannot be hardened through traditional quenching like higher-carbon steels, it can be carburized to improve surface hardness.
This heat treatment process allows manufacturers to create components with a hard exterior and a ductile core—ideal for parts subject to surface wear but needing internal toughness.
1020 steel also responds well to annealing, normalizing, and stress-relief processes, which improve machinability and reduce internal stresses.
7. Machinability and Weldability
Among the most appreciated 1020 steel properties are its machinability and weldability. With a machinability rating of 65% (compared to B1112), it’s relatively easy to cut, drill, or mill. The material produces minimal tool wear and ensures smooth finishing.
As for weldability, 1020 steel is exceptional. Its low carbon content ensures fewer issues during welding processes like MIG, TIG, or arc welding. This makes it a preferred choice for industries where customized fabrication is required.
Real-World Applications of 1020 Steel
Thanks to its combination of favorable 1020 steel properties, this material finds applications across a wide spectrum of industries. These include:
- Automotive: axles, shafts, and gear components
- Construction: support beams, tubing, and brackets
- Machinery: rollers, bushings, and spindles
- Agricultural tools and equipment
- Furniture frames and fixtures
Its ease of processing also means it can be quickly manufactured in bulk, lowering production costs without sacrificing performance.
Comparison with Other Steel Grades
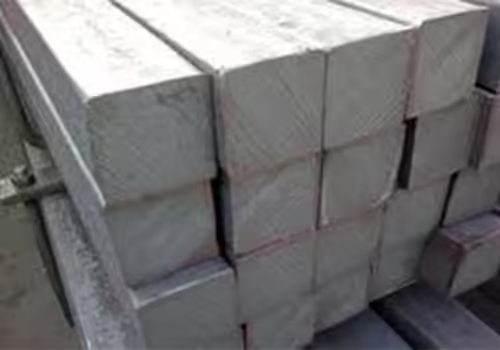
To fully appreciate 1020 steel properties, it helps to compare it with similar grades:
- 1018 Steel: Slightly lower carbon content, better suited for precision machining, but less hardenable than 1020.
- 1045 Steel: Higher carbon content, offering greater strength and wear resistance, but reduced machinability and ductility.
- 4140 Steel: An alloy steel with chromium and molybdenum, offering superior strength, hardness, and corrosion resistance, but at a higher cost.
While each has its place, 1020 steel is often chosen when a cost-effective, easily machinable material is needed with a balance of strength and formability.
Conclusion
1020 steel properties make it an outstanding choice for many mechanical and structural applications. Its unique combination of strength, ductility, and ease of fabrication make it one of the most versatile low-carbon steels in use today.
From its excellent weldability and machinability to its suitability for carburizing and heat treatments, 1020 steel continues to be a favorite across industries. Understanding these core properties ensures that engineers and manufacturers can make informed decisions that align with performance and budgetary goals.
If you’re considering a material that offers flexibility without compromising on quality, 1020 steel is a top contender.
FAQ
What is the difference between 1020 steel and 1018 steel?
The primary difference lies in their carbon content. 1020 steel contains slightly more carbon than 1018, resulting in higher strength but slightly less ductility. 1018 is generally preferred for precision machining, while 1020 offers better wear resistance.
Can 1020 steel be hardened?
1020 steel cannot be hardened through conventional quenching due to its low carbon content. However, it can be carburized to create a hard surface layer while retaining a ductile core.
Is 1020 steel good for welding?
Yes, one of the most significant 1020 steel properties is its excellent weldability. It can be welded using various methods without requiring complex pre- or post-weld treatments.
How does 1020 steel perform in high temperatures?
1020 steel maintains its mechanical properties up to moderate temperatures. However, for extremely high-temperature applications, alloy steels are generally more appropriate.
Is 1020 steel suitable for structural applications?
Yes, it is widely used in structural frameworks and components due to its strength, machinability, and affordability. However, protective coatings are recommended if the material will be exposed to corrosive environments.