
42CrMo4 vs 4140: Which Steel is Stronger for Heavy Use?
Table of Contents
Introduction
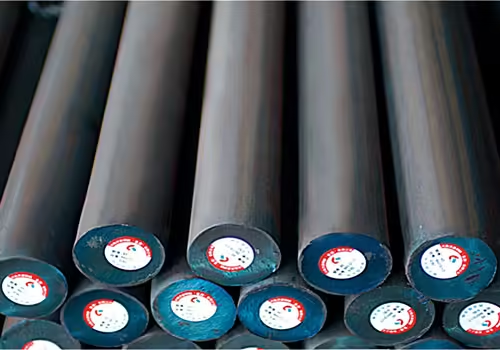
When choosing materials for critical engineering and industrial purposes, the debate around 42CrMo4 vs 4140 often arises. These two high-performance alloy steels are widely used in industries that demand strength, durability, and excellent mechanical performance. The comparison of 42CrMo4 vs 4140 is especially relevant for sectors like automotive manufacturing, machinery production, oil and gas, and heavy construction, where material failure is not an option.
While both steels offer a blend of strength and toughness, they are standardized under different systems—42CrMo4 following the European EN standards, and 4140 conforming to the American AISI classification. Despite the similarity in alloying elements, their performance under stress, resistance to fatigue, and adaptability in various environmental conditions can differ significantly. In this comprehensive guide, we’ll explore the detailed comparison of 42CrMo4 vs 4140, aiming to help engineers and procurement specialists make more informed decisions.
Understanding how 42CrMo4 vs 4140 compare in chemical composition, mechanical performance, and application efficiency is critical for projects requiring long-term reliability. Choosing the right material isn’t just a matter of compliance—it’s a strategic decision that affects cost, performance, and safety.
Understanding the Basics of 42CrMo4 and 4140 Steel
To fully grasp the importance of the 42CrMo4 vs 4140 comparison, one must first understand their origins and base characteristics. 42CrMo4 is a low-alloy steel from the EN 10083-3 European standard. It is primarily alloyed with chromium and molybdenum, two elements that give it increased hardenability, high tensile strength, and excellent impact resistance even under high-stress conditions. It is often favored in Europe for its reliability in powertrain components, shafts, and structural parts exposed to dynamic loading.
4140, on the other hand, is a chromium-molybdenum alloy steel under the AISI (American Iron and Steel Institute) system. It is one of the most commonly used steels in North America due to its balance of strength, machinability, and cost-effectiveness. Like 42CrMo4, it is heat-treatable and demonstrates good toughness and wear resistance. However, its material characteristics may vary slightly based on local processing standards and conditions.
Despite their similar chemical structure, the practical comparison of 42CrMo4 vs 4140 often hinges on localized performance, processing options, and end-use requirements. Understanding these differences can make a significant impact on equipment longevity and performance in harsh environments.
Chemical Composition Overview
The most fundamental starting point in the 42CrMo4 vs 4140 comparison is their chemical composition. Both steels contain similar alloying elements such as chromium (Cr), molybdenum (Mo), carbon (C), and manganese (Mn), which are responsible for their enhanced mechanical characteristics. However, subtle differences in percentage composition can lead to meaningful changes in performance.
Typically, 42CrMo4 contains slightly higher levels of chromium compared to 4140, giving it potentially better corrosion resistance and wear performance in certain industrial settings. Additionally, carbon content in 4140 tends to be on the higher end of the scale, slightly improving its hardness and tensile strength but potentially reducing weldability.
These minor differences become more pronounced when the materials are subjected to processes such as heat treatment, quenching, or tempering. For engineers, this means the choice between 42CrMo4 vs 4140 should also account for the intended manufacturing process and final application environment.
By examining the exact elemental breakdown, professionals can determine which steel is better suited for specific purposes—whether that’s resistance to corrosion, ability to undergo complex machining, or enhanced fatigue life under repeated load.
Mechanical Properties: 42CrMo4 vs 4140 in Focus
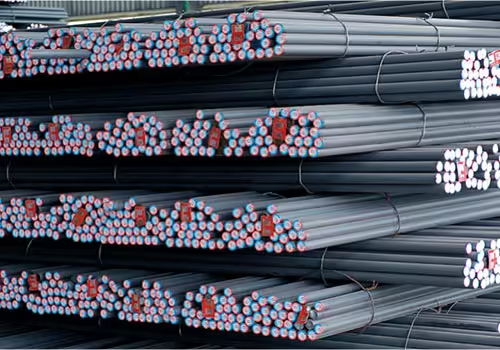
One of the key areas of focus in the 42CrMo4 vs 4140 comparison is their mechanical properties. This is where practical performance data plays a vital role, especially for applications involving high loads, impacts, or extreme temperatures.
Both 42CrMo4 and 4140 demonstrate high tensile and yield strength, making them ideal for demanding components like crankshafts, gears, and connecting rods. However, when subjected to rigorous mechanical testing, differences begin to emerge.
For instance, 4140 typically offers a slightly higher tensile strength in its quenched and tempered state, which makes it appealing for applications where static load-bearing is prioritized. In contrast, 42CrMo4 often shows superior toughness and fatigue resistance, making it more suitable for parts exposed to cyclical stress and vibration.
Here, choosing between 42CrMo4 vs 4140 becomes a decision of trade-offs—prioritizing certain mechanical benefits over others depending on the end-use. The detailed performance specifications, such as elongation at break, impact energy (Charpy V-notch), and Brinell hardness, provide deeper insights that help in finalizing the right material for your needs.
Key Mechanical Comparisons
Property | 42CrMo4 | 4140 |
---|---|---|
Standard | EN 10083-3 | AISI/SAE |
Yield Strength | 930 MPa (quenched + tempered) | 655 MPa (quenched + tempered) |
Tensile Strength | 1000–1100 MPa | 850–1000 MPa |
Elongation at Break | ~14% | ~25% |
Hardness (HB) | 248–302 | 197–235 |
Machinability | Moderate | Good |
Weldability | Limited (requires preheat) | Limited (requires preheat) |
From the table, we can observe that 42CrMo4 generally offers higher strength and hardness compared to 4140. However, 4140 shows better elongation at break, indicating more flexibility and toughness in some scenarios.
Industrial Applications and Use Cases
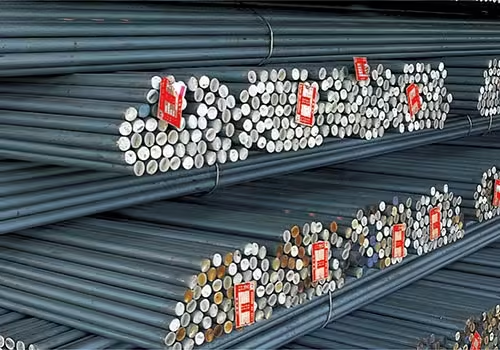
A direct comparison of 42CrMo4 vs 4140 wouldn’t be complete without a detailed analysis of where each steel truly excels in practical, real-world scenarios. While the two alloy steels share many overlapping properties—such as strength, hardenability, and wear resistance—their performance can vary significantly depending on the specific industrial context in which they are applied.
Both 42CrMo4 and 4140 are used across a broad range of heavy-duty applications, including automotive engineering, oil and gas drilling equipment, mechanical gear systems, and high-load structural components. However, due to differences in regional standards, supply chains, and heat treatment preferences, certain industries may lean more heavily toward one material over the other.
For example, European manufacturers might favor 42CrMo4 because of its compliance with EN standards and its well-documented track record in European mechanical systems and powertrain applications. On the other hand, industries based in North America often opt for 4140, as it aligns more closely with AISI and ASTM standards, and is widely available in local markets.
In this light, understanding the application-specific advantages of 42CrMo4 vs 4140 is crucial for selecting the right material. Factors such as service environment, expected load cycles, machinability, and post-processing methods all influence which steel offers better long-term performance and economic value in a given scenario.
Common Uses of 42CrMo4
- High-performance automotive parts such as crankshafts, gears, and axle shafts
- Heavy machinery components
- Structural parts exposed to high static and dynamic stress
- High-pressure tubing
Common Uses of 4140
- Oil and gas drilling equipment
- Agricultural machinery parts
- Fasteners and bolts in structural frameworks
- Hydraulic systems and shafts
In environments requiring higher tensile strength and abrasion resistance, 42CrMo4 might be preferred. Conversely, for applications where ductility and machinability are crucial, 4140 could be the better choice.
Heat Treatment Capabilities
Another factor that heavily influences the debate of 42CrMo4 vs 4140 is their behavior under heat treatment. Both materials respond well to quenching and tempering processes, enhancing their mechanical performance.
- 42CrMo4: Achieves excellent hardness and strength through quenching and tempering, suitable for extreme mechanical loads.
- 4140: Offers a good balance of toughness and wear resistance after similar treatment, often used where fatigue resistance is critical.
The heat treatment potential of both steels makes them versatile choices, but differences in strength outcomes could guide your selection based on end-use needs.
Cost and Availability Factors
When making material decisions, cost and availability often play a critical role. Although both steels are considered mid-range in price compared to high-alloy or tool steels, regional standards and supplier options may affect procurement.
- In Europe, 42CrMo4 may be more readily available and cost-effective.
- In North America, 4140 is usually easier to source, often making it the default choice in U.S.-based operations.
Assessing your local supply chain is essential when weighing the pros and cons of 42CrMo4 vs 4140 for large-scale manufacturing.
Weldability and Machinability in Practice
Although both steels are known for their strength, they are not the easiest to weld. Preheating and post-weld heat treatments are typically necessary to avoid cracking or brittleness.
- 42CrMo4: Requires controlled heating cycles to maintain toughness.
- 4140: While still requiring preheating, it is generally easier to machine and weld than 42CrMo4.
These traits might influence your choice, especially in projects involving complex assemblies or frequent modifications.
Performance in Extreme Environments
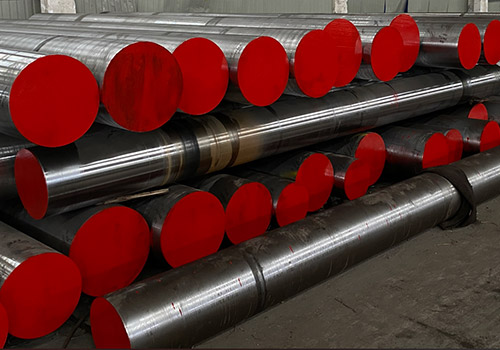
Performance under stress, temperature fluctuations, and exposure to corrosive elements are key benchmarks when comparing 42CrMo4 vs 4140.
- 42CrMo4: Performs better under extreme mechanical loads and provides enhanced wear resistance.
- 4140: Exhibits good performance in fatigue-prone and corrosive environments but may fall short in extremely high-stress applications.
Selecting the ideal steel for such settings depends on whether maximum load endurance or longer fatigue life is prioritized.
Conclusion
The decision between 42CrMo4 vs 4140 ultimately depends on your specific application needs. If your priority is achieving higher tensile strength and durability for heavy-duty equipment, 42CrMo4 is likely the better option. However, if you value ease of machining, cost-efficiency, and good overall performance, 4140 could be your ideal choice. Each steel has unique benefits that make it well-suited for different environments and manufacturing processes. Careful evaluation of mechanical properties, availability, and application requirements will guide you toward the optimal selection.
FAQ
What are the main chemical differences between 42CrMo4 and 4140?
The primary difference lies in the slight variation in chromium and molybdenum content. 42CrMo4 typically has slightly higher chromium, which may offer marginally better corrosion resistance.
Is 42CrMo4 more durable than 4140?
Yes, in many high-stress applications, 42CrMo4 demonstrates superior tensile strength and hardness, making it more durable for heavy-duty use.
Which is easier to machine: 42CrMo4 or 4140?
4140 is generally easier to machine due to its composition and structure. This can reduce machining time and costs.
Can both steels be welded easily?
Neither steel is ideal for welding without proper preparation. Both require preheating and sometimes post-weld heat treatment to ensure structural integrity.
Which steel is better for automotive applications?
Both are used in automotive parts, but 42CrMo4 is often chosen for components requiring higher strength and wear resistance, such as gears and axle shafts.