
Ultimate Showdown: 4130 Steel or 4140? 5 Winners
Table of Contents
Introduction
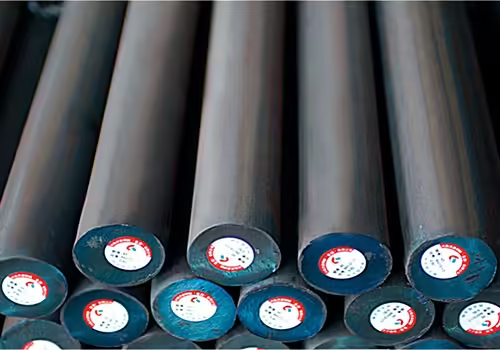
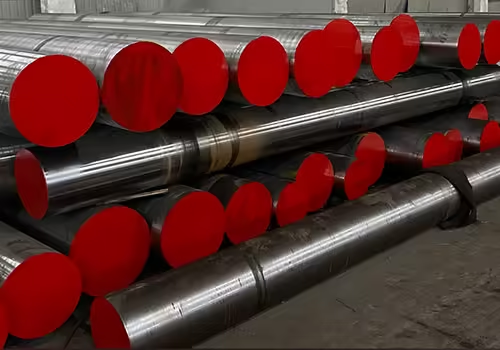
When comparing 4130 steel or 4140, both are incredibly versatile alloys with a variety of applications across different industries, including automotive, aerospace, and manufacturing. However, the question often arises: which one is better for your specific needs? This article will dive into the critical aspects of 4130 steel or 4140, highlighting their properties, differences, advantages, and ideal use cases. By the end, you’ll have a clearer understanding of which alloy best fits your project.
Steel alloys come in various grades, each engineered for specific properties to meet the demands of different applications. Among these, 4130 steel or 4140 are both popular choices for applications requiring strength, toughness, and wear resistance. They both belong to the group of low-alloy steels, but what sets them apart? This comparison will examine the composition, physical properties, performance, and practical applications of 4130 steel or 4140 to help guide your selection process.
Chemical Composition: A Key to Their Differences
The primary difference between 4130 steel or 4140 lies in their chemical composition. Both alloys are made from carbon, chromium, and molybdenum, but in varying proportions, which directly impacts their performance and processing capabilities.
- 4130 steel: This is a chromium-molybdenum alloy with a lower carbon content (approximately 0.30%), making it easier to weld and shape. It contains around 0.8% chromium and 0.15% molybdenum.
- 4140 steel: Slightly stronger due to its higher carbon content (approximately 0.40%), 4140 steel has a more significant presence of chromium and molybdenum. This increased carbon content enhances its hardenability and overall strength.
These differences in chemical composition influence not only the strength of 4130 steel or 4140 but also their response to heat treatment processes such as quenching and tempering.
Properties and Performance: Which Alloy Wins?
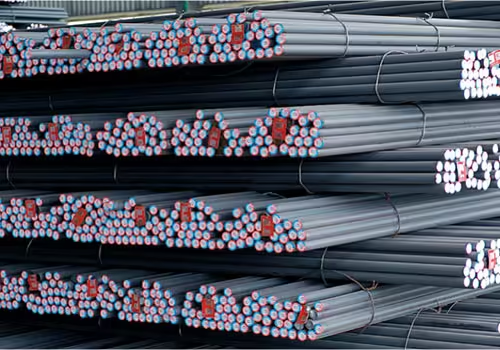
Strength and Hardness
When comparing the strength of 4130 steel or 4140, 4140 steel takes the lead due to its higher carbon content, which allows it to achieve higher tensile strength and hardness. This makes 4140 steel more suitable for applications that require superior wear resistance and heavy-duty performance under mechanical stress.
However, 4130 steel still offers excellent strength for many applications, particularly when a balance between strength and ductility is required.
Toughness and Durability
Both 4130 steel or 4140 exhibit good toughness and impact resistance. However, 4130 steel tends to be slightly more ductile than 4140 steel, making it a better choice in applications where the material needs to absorb energy without cracking or breaking.
4140 steel, with its higher carbon content and better hardenability, offers enhanced wear resistance, making it a top contender for parts exposed to high friction and extreme conditions.
Machinability
While 4130 steel is easier to machine due to its lower carbon content, 4140 steel is more challenging to work with. However, 4140 can be heat-treated to a higher hardness, making it ideal for parts that need to maintain their shape and performance under extreme stress.
When selecting between 4130 steel or 4140, consider the level of machining difficulty your project can accommodate. For quick fabrication and moderate performance, 4130 steel excels. For critical parts requiring high durability, 4140 steel is the better option.
Applications: Where Are 4130 and 4140 Used?
Both 4130 steel and 4140 steel have a wide range of uses, but their properties make them better suited for different tasks:
- 4130 steel: Commonly used in the automotive and aerospace industries for parts such as aircraft components, gears, and frames. It is also a popular choice for making bicycle frames, roll cages, and other high-strength, low-weight applications.
- 4140 steel: Known for its exceptional strength, 4140 steel is often used in applications like crankshafts, gears, and axle components. Its ability to withstand higher stresses makes it ideal for heavy-duty industrial applications, such as oil rigs, mining equipment, and machinery parts.
Table: 4130 Steel vs 4140 – Key Comparisons
Property/Feature | 4130 Steel | 4140 Steel |
---|---|---|
Carbon Content | 0.30% | 0.40% |
Chromium Content | 0.80% | 0.90% |
Molybdenum Content | 0.15% | 0.20% |
Tensile Strength | 90,000-100,000 psi | 95,000-110,000 psi |
Hardness | 28-32 HRC | 28-35 HRC |
Applications | Aerospace, automotive | Heavy machinery, gears |
Machinability | Good | Moderate |
Toughness | High | Higher |
About Henan Jiyuan Iron & Steel (Group) Co., Ltd.
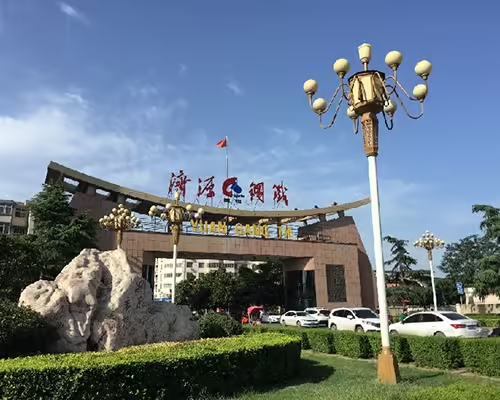
Henan Jiyuan Iron & Steel (Group) Co., Ltd., founded in 1958, is one of China’s leading steel enterprises. Recognized as a national high-tech enterprise, the company is listed among the Top 500 Chinese Enterprises and Top 100 Global Iron and Steel Enterprises. Located in Jiyuan City, Henan Province, the company benefits from excellent transportation access, with direct connections to dedicated railway lines.
With more than 8,000 employees, including 3,000 professional and technical personnel, and total assets of CNY 25 billion, the company is a major player in the steel industry. We specialize in producing and selling high-quality special steels such as carbon steel bars, alloy steel bars, and bright steel materials.
Our popular grades include Q195, Q235, 1045, 4130, 4140, 42CrMo4, SCM440, SAE8620H, and more, in diameters ranging from φ12 to φ300. Whether you’re looking for high-strength round bars or custom steel solutions, we have the capacity and expertise to meet your requirements.
If you’re deciding between 4130 steel vs 4140 or need expert advice on steel selection, don’t hesitate to contact us. We’re here to help you choose the best material for your application.
Conclusion
Choosing between 4130 steel or 4140 depends entirely on your project’s specific requirements. 4130 steel or 4140 both offer excellent mechanical properties, but their performance varies depending on the application. If you need a material that is easier to weld and machine, 4130 steel is often more suitable, especially for lightweight structures and general-purpose components.
However, if your application involves high stress, impact, or wear, then 4140 steel is typically the better option. With higher carbon content and improved hardenability, 4140 steel can withstand tougher conditions and is commonly used in heavy-duty equipment.
In short, whether you choose 4130 steel or 4140, your decision should be based on strength requirements, fabrication methods, and cost considerations. Both alloys are reliable, but the right choice will ensure better performance and longer service life.
FAQ
Can 4130 steel be used for heavy-duty applications?
4130 steel is known for its versatility, weldability, and decent strength, making it a popular choice in many structural and performance-based designs. However, when it comes to extremely heavy-duty applications—such as those found in mining, high-load transportation, or powertrain systems—4130 steel may fall short in long-term wear resistance and strength. If your engineering design involves continuous stress, high torque, or impact-heavy operations, then 4140 might be a better choice. When deciding between 4130 steel or 4140, it’s important to consider the mechanical load expectations of your project.
Is 4140 steel easier to weld than 4130 steel?
No, welding 4140 steel requires more care and preparation compared to 4130. This is primarily due to the higher carbon content in 4140 steel, which makes it more susceptible to cracking during and after welding. Proper preheating and post-weld heat treatment are often necessary to ensure structural integrity. In contrast, 4130 steel can usually be welded without preheating and is often chosen for applications where fabrication efficiency and ease of assembly are critical. When evaluating 4130 steel or 4140 for weldability, 4130 is typically the easier and more cost-effective option.
How do the costs compare between 4130 steel and 4140 steel?
Cost is a significant factor in material selection, especially for large-scale manufacturing or construction projects. In general, 4130 steel is slightly less expensive than 4140 due to its lower alloy content and less demanding processing requirements. However, choosing between 4130 steel or 4140 should go beyond just price. While 4140 may have a higher initial cost, its improved performance in high-stress environments may offer better long-term value through reduced maintenance and replacement cycles. Therefore, it’s essential to consider total lifecycle costs when making a selection.
Can both 4130 and 4140 steel be heat treated?
Yes, both 4130 steel and 4140 steel can undergo various heat treatment processes to enhance their mechanical properties. Heat treatment options such as quenching, tempering, and normalizing can improve hardness, strength, and toughness in both alloys. However, when comparing 4130 steel or 4140, the latter exhibits a higher hardenability, allowing it to reach greater levels of hardness and strength. This makes 4140 more suitable for applications requiring high surface hardness and excellent wear resistance. In contrast, 4130 is often used when moderate hardness with better ductility is required.
Which steel is more suitable for making gears?
Gears are components that require high tensile strength, good fatigue resistance, and strong surface hardness to withstand continuous friction and torque. Between 4130 steel or 4140, 4140 steel is the better candidate for gear production. Its superior strength, wear resistance, and hardenability make it ideal for use in heavy-duty gear systems used in construction equipment, trucks, and industrial machinery. While 4130 steel may be used in some light- to medium-duty gear applications, it generally lacks the robustness needed for high-performance or long-life gear sets.