
Is 4140 Steel Weldability a Dealbreaker?
Table of Contents
Introduction
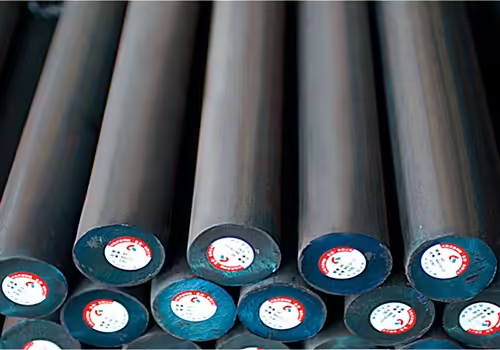
When it comes to selecting the right material for a structural or mechanical application, weldability is often a key consideration. One alloy that frequently enters the conversation is 4140 steel. Known for its strength, hardenability, and resistance to fatigue, 4140 steel is a chromium-molybdenum alloy steel often used in the automotive, aerospace, and oil & gas industries. However, discussions about 4140 steel weldability continue to generate mixed opinions.
In this article, we’ll explore the factors affecting 4140 steel weldability, common challenges, best practices for welding, and whether or not its characteristics make it a dealbreaker for critical projects. We will also provide a comparative table to better illustrate its welding compatibility against other common steels.
What is 4140 Steel?
414140 steel is a versatile chromium-molybdenum alloy steel renowned for its remarkable strength, toughness, and resistance to wear. It falls under the AISI (American Iron and Steel Institute) classification, commonly referred to as AISI 4140. The steel is part of the family of low alloy steels but distinguishes itself through its balanced composition and heat treatment adaptability.
Chemical Composition of 4140 Steel:
- Carbon: 0.38–0.43%
- Chromium: 0.80–1.10%
- Molybdenum: 0.15–0.25%
- Manganese: 0.75–1.00%
- Silicon: 0.15–0.35%
Key Characteristics:
- High tensile strength: Enables it to withstand substantial mechanical loads.
- Good fatigue strength: Well-suited for cyclic loading, such as rotating parts.
- Excellent toughness: Maintains structural integrity even under impact.
- Wear resistance: Resists deformation and surface damage over time.
These mechanical properties make it a popular material in a wide array of industrial applications, including:
- Automotive (e.g., crankshafts, axle shafts)
- Oil and gas (e.g., drill collars, tool joints)
- Aerospace (e.g., landing gear)
- Heavy equipment (e.g., shafts, gears, bushings)
However, while 4140 steel is excellent in performance, its weldability is often scrutinized, especially in high-stakes environments where joint failure can lead to catastrophic consequences.
Why is 4140 Steel Weldability Often Questioned?
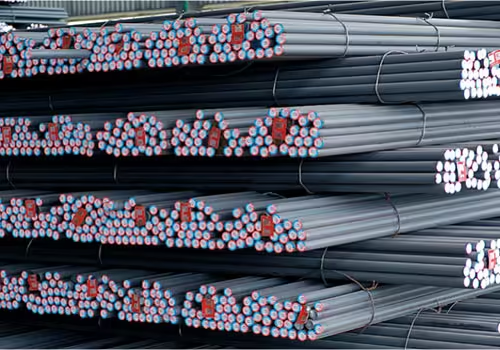
The weldability of a material refers to its ability to be joined to another piece using a welding process without compromising structural integrity. In the case of 4140 steel, the issue stems from its chemical makeup and hardenability.
Key Reasons 4140 Steel Weldability is Challenging:
- High Carbon Equivalent (CE):
- The carbon equivalent value (CE) of 4140 is relatively high due to its alloying elements.
- A higher CE increases the steel’s hardenability, which in turn raises the risk of cracking during welding.
- Heat-Affected Zone (HAZ) Hardening:
- When welded, 4140 steel tends to harden in the HAZ, especially without proper preheating or post-weld treatment.
- This hardening can make the steel brittle and susceptible to cracking under stress.
- Hydrogen-Induced Cracking:
- The presence of hydrogen during welding can cause delayed cracking. This is particularly concerning in steels with high hardness in the HAZ.
- Dimensional Instability:
- During the thermal cycles of welding, the part can experience distortion or warping due to uneven expansion and contraction.
- Requirement for Tight Control of Parameters:
- Precise control of temperature, filler material, and cooling rate is crucial for success, making the process complex and error-prone.
Because of these factors, some engineers opt to avoid welding 4140 steel when simpler alternatives are available. In applications requiring welding, the risks must be thoroughly managed.
Welding Techniques to Improve 4140 Steel Weldability
4140 steel, a chromium-molybdenum alloy steel, is widely known for its excellent strength, hardness, and wear resistance. However, these same properties make it challenging to weld. Its high carbon content and alloying elements increase the risk of cracking—particularly in the heat-affected zone (HAZ). Despite these challenges, successful welding of 4140 steel is achievable by implementing specific welding techniques and adhering to precise thermal management practices.
Preheating
Preheating 4140 steel is one of the most critical steps in minimizing weld-related cracking. The goal of preheating is to reduce the temperature differential between the weld zone and the base metal, thus minimizing thermal shock.
- Recommended Preheat Range: 400°F to 600°F (204°C to 316°C)
- Why It’s Important:
- Reduces residual stresses during welding.
- Prevents rapid cooling, which can lead to hard, brittle microstructures.
- Enhances hydrogen diffusion, decreasing the chance of hydrogen embrittlement.
Preheating should be uniform across the entire workpiece. Infrared thermometers or thermal crayons can help verify that target temperatures are achieved and maintained consistently throughout the welding process.
Post-Weld Heat Treatment (PWHT)
After welding, the material often retains internal stresses and potentially undesirable microstructures. Post-weld heat treatment (PWHT) is essential for restoring ductility and mechanical performance in welded 4140 steel.
- Typical PWHT Range: Tempering at 1,100°F to 1,300°F (593°C to 704°C)
- Benefits of PWHT:
- Relieves residual stresses induced during welding and cooling.
- Reduces hardness in the HAZ to improve toughness and crack resistance.
- Enhances the overall dimensional stability of the component.
The specific PWHT parameters depend on factors like part thickness, intended service conditions, and weld geometry. It’s vital to cool the part slowly to room temperature post-PWHT to avoid reintroducing stress.
Proper Filler Selection
Selecting the appropriate filler metal is crucial to ensure compatibility between the weld and the base material. For 4140 steel, the filler must be capable of matching the base metal’s strength while also offering good ductility and toughness.
- Recommended Filler: ER80S-D2
- Key Considerations:
- Filler metals should provide a weld deposit with mechanical properties equal to or better than the base metal.
- Over-matching strength is not always beneficial; it can lead to reduced ductility or increased brittleness.
- Filler wire chemistry should be chosen to minimize dilution issues and cracking susceptibility.
In some applications, nickel-based or low-alloy fillers may also be appropriate to accommodate specific service requirements like impact resistance or temperature resilience.
Controlled Cooling
Once the weld is completed, slow and controlled cooling is critical to prevent the formation of hard martensitic structures that can lead to delayed cracking.
- Cooling Best Practices:
- Allow the part to cool in still air if the ambient temperature is moderate.
- In colder environments, wrapping the part in an insulating blanket may be necessary.
- Avoid forced air or water quenching, as these induce thermal shock and structural imbalances.
Cooling rates directly influence the microstructure in the HAZ. Controlled cooling allows for the formation of more ductile phases such as bainite or tempered martensite instead of brittle martensite.
Low-Hydrogen Electrodes
Utilizing low-hydrogen electrodes (e.g., E7018) helps prevent hydrogen-induced cracking, a common issue with high-strength steels.
Comparing 4140 Steel Weldability to Other Steels
To better understand how 4140 steel weldability stacks up against other common steels, the following table outlines a comparison based on weldability, preheat requirements, and typical applications.
Steel Type | Weldability | Preheat Required | Typical Applications |
---|---|---|---|
4140 Steel | Moderate | Yes | Gears, Shafts, Structural Components |
A36 Carbon Steel | Excellent | No | Structural Beams, Bridges, Construction |
1018 Mild Steel | Excellent | No | Machined Parts, Fasteners |
1045 Medium Steel | Good | Yes (Mild) | Axles, Bolts, Studs |
Stainless 304 | Excellent | No | Food Processing, Marine Components |
From this table, it is evident that while 4140 steel offers mechanical advantages, its weldability does not match the ease of more conventional steels.
Practical Applications Where 4140 Steel Weldability Matters
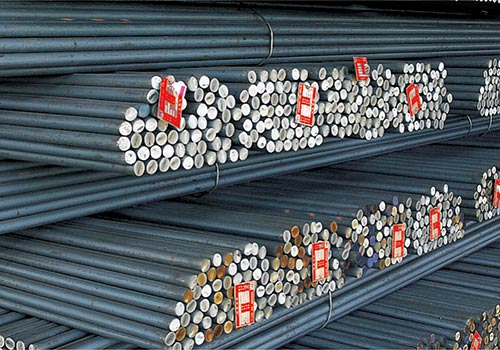
Despite the challenges associated with 4140 steel weldability, this alloy remains a cornerstone in industries that demand high performance under stress, wear, and extreme mechanical loads. Thanks to its unique balance of strength, hardness, and fatigue resistance, 4140 steel is widely adopted across sectors. However, its weldability must always be considered during design and repair to ensure long-term reliability.
Below are several real-world applications where 4140 steel weldability plays a crucial role in achieving optimal performance:
Heavy Machinery
In the construction and mining industries, 4140 steel is frequently used for critical components such as drive shafts, gears, axles, couplings, and lifting arms. These parts are often subjected to cyclic loading and shock impact. In such cases, 4140 steel weldability is vital during both fabrication and repair.
- Welds must be precisely executed to avoid creating stress risers.
- Preheating and post-weld treatments ensure the mechanical properties are preserved.
- Controlled welding processes prevent hard zones that could lead to fatigue failure.
The weldability of 4140 steel ensures that heavy machinery can be serviced in the field, extending equipment lifespan and reducing costly downtime.
Automotive Parts
In automotive manufacturing and repair, components such as crankshafts, connecting rods, suspension parts, and steering knuckles often use 4140 steel due to its exceptional strength-to-weight ratio.
- When welding these parts, 4140 steel weldability becomes a determining factor in safety and structural integrity.
- Poor welding techniques can compromise the entire vehicle system.
- Skilled welding ensures seamless performance even under high-speed rotational stress.
In high-performance vehicles and motorsports, 4140 steel weldability enables custom modifications and reinforcements without sacrificing durability.
Tool and Die Industry
The tool and die industry relies heavily on 4140 steel for making tool holders, forming dies, molds, and precision jigs. These components often undergo maintenance and modification, which involves welding.
- 4140 steel weldability ensures tools can be refurbished rather than replaced, saving time and resources.
- Weld repairs are carefully executed to retain exact dimensions and surface finishes.
- Advanced welding techniques reduce the risk of hardening or warping, which is critical for precision tooling.
Here, the weldability of 4140 steel is not just a convenience—it’s essential for maintaining tolerances and tool functionality in high-stakes manufacturing environments.
Oil & Gas Equipment
In the oil and gas industry, equipment such as downhole tools, drill collars, valve bodies, and pressure control systems are subject to extreme conditions—high pressure, corrosive environments, and mechanical shock.
- The weldability of 4140 steel plays a pivotal role in manufacturing and maintaining these components.
- Substandard welding can lead to catastrophic failures in high-pressure environments.
- High-strength welds, achieved through controlled processes and low-hydrogen electrodes, allow 4140 steel to perform reliably over time.
As a result, 4140 steel weldability directly impacts safety, operational continuity, and compliance with regulatory standards in the energy sector.
Tips for Avoiding Failures Due to Poor Welding
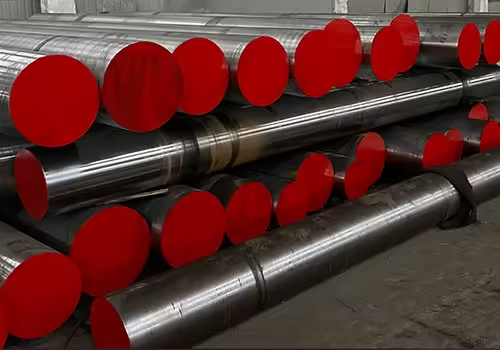
If you’re planning to work with 4140 steel, here are actionable tips to avoid welding issues:
- Always preheat and maintain temperature during the welding process
- Select a filler metal that matches the mechanical properties
- Perform PWHT to reduce residual stresses
- Use a qualified welding procedure specification (WPS)
- Monitor for signs of cracking or brittleness after welding
Conclusion
The answer depends on the application and the level of welding expertise available. While 4140 steel weldability is more complex than many other steels, it is not necessarily a dealbreaker. With proper preparation, suitable filler materials, and heat treatment processes, successful welds can be achieved.
However, for high-stakes applications where welding must be simple and quick, 4140 steel may not be the best choice. Understanding the nuances of this material allows engineers and welders to make informed decisions about its suitability.
FAQ
What is the main challenge of welding 4140 steel?
The main challenge is controlling the heat-affected zone to prevent hardening and cracking.
Can 4140 steel be welded without preheating?
It is not recommended. Preheating is essential to avoid cracking.
What filler material is best for welding 4140 steel?
ER80S-D2 or similar low-alloy, high-strength fillers are commonly used.
Is post-weld heat treatment always necessary?
For critical applications, yes. PWHT helps relieve stress and reduce brittleness.
Can beginners weld 4140 steel?
Due to its complexity, 4140 steel is better suited to experienced welders using controlled environments.