
Billet of Steel: 6 Critical Reasons to Avoid Bad Quality
Table of Contents
Introduction
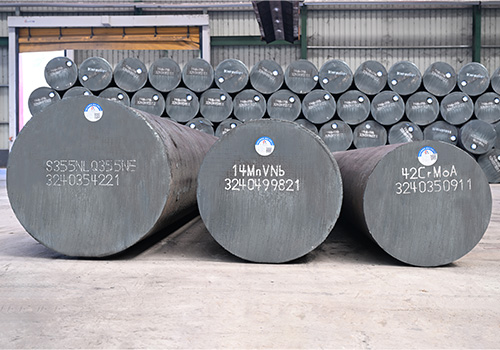
When it comes to industrial manufacturing and heavy machinery, the billet of steel forms the foundational element of many components. The quality of the billet of steel determines the durability, strength, and performance of the final product. From automotive parts to construction materials, using a high-quality billet of steel is not just a preference—it is a necessity. Conversely, using a substandard or bad billet of steel can lead to catastrophic failures, increased costs, and safety concerns.
In this article, we will explore six critical reasons why you should always avoid using a bad billet of steel in your operations. We will dive into the effects of poor material selection, how to identify inferior products, and what makes a billet of steel truly reliable.
NO 1. Structural Integrity Is Compromised
In any industrial or mechanical application, the strength of a product starts at the raw material level. Among the most crucial materials in metalworking and construction is the semi-finished steel product typically used as the base form for rolled and forged goods. When the internal structure of this foundational component lacks homogeneity, it leads to significant integrity issues down the line.
Inferior batches may contain microscopic cracks, slag inclusions, or gas pockets that compromise load-bearing capacity. These inconsistencies often escape basic inspection but will inevitably reveal themselves under thermal cycling, pressure, or dynamic stress during use. For instance, equipment components such as shafts or support beams that rely on consistent mechanical strength can fail unexpectedly if their structural core is flawed.
Such failures are not just costly—they’re dangerous. A misformed piece can trigger cascading mechanical damage or even full-system breakdowns. That’s why rigorous testing, including ultrasonic scanning and composition analysis, is essential when sourcing raw metal units for critical applications. Trusting material without thorough quality checks can turn a minor flaw into a major liability.
NO 2. Poor Billet Quality Leads to Manufacturing Defects
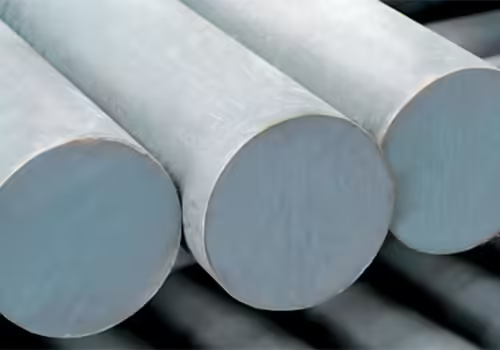
The entire manufacturing workflow—whether it’s forging, hot rolling, CNC machining, or thermal treatment—relies heavily on the consistency and reliability of its foundational inputs. When the primary steel stock used in forming components lacks metallurgical uniformity, a wide range of complications can emerge throughout the production chain.
Substandard metal blanks often contain internal defects such as shrinkage cavities, gas porosity, or segregated phases. These imperfections are frequently invisible during visual inspection but become evident once the material is subjected to mechanical stress, deformation, or thermal processing. For instance, during forging, internal voids may expand unevenly, causing deformed or cracked sections that are difficult to salvage.
Chemical consistency is another critical factor. Inputs with unbalanced concentrations of elements like sulfur, phosphorus, or carbon can introduce brittleness, reduce ductility, or create hard spots that interfere with machining. Even small variations in alloy composition can disrupt downstream processes by shifting mechanical properties such as hardness, yield strength, or fatigue resistance outside acceptable tolerances.
Problems also arise during machining and cutting operations. Uneven grain structures or coarse crystallization within the raw material can cause unpredictable behavior under cutting tools, leading to excessive tool wear, vibration, burrs, or misalignment. In precision manufacturing—such as in aerospace or automotive sectors—these inconsistencies can compromise dimensional accuracy, surface finish, and tolerances, resulting in rejected parts and costly rework.
The surface condition of raw steel sections further contributes to production efficiency. Oxide layers, rust, or inclusion streaks on the exterior can interfere with tool engagement, increase friction, and shorten the lifespan of machining tools. Moreover, these surface flaws may reduce the adherence of coatings, paints, or platings, affecting the corrosion resistance of the final product.
All these issues lead to operational inefficiencies. Production teams may need to run extra quality checks, extend machining cycles, or replace tools more frequently. Line interruptions, bottlenecks, and increased maintenance all contribute to rising overheads. In some cases, entire batches may require scrapping or reprocessing, pushing back delivery schedules and increasing material waste.
For manufacturers working within regulated environments—such as aerospace, medical, or energy industries—the consequences of inferior material quality are even more severe. Non-conforming batches can trigger compliance failures, revoke certifications, or result in the rejection of large-scale orders. In industries where traceability and uniformity are non-negotiable, accepting lower-grade steel inputs poses serious risks to long-term viability.
There are also downstream consequences for the business. Product recalls, warranty claims, or negative customer reviews can originate from poor-quality input stock. One misjudgment in material procurement can damage brand reputation, drive up service costs, and reduce customer loyalty. In this sense, the initial cost savings from using cheaper raw materials are quickly outweighed by the cumulative financial losses over time.
In conclusion, starting with high-quality raw steel forms isn’t just a technical preference—it’s a strategic necessity. Avoiding defective input materials protects the consistency of manufacturing processes, ensures compliance, and preserves the integrity of the final product.
NO 3. Reduced Product Lifespan and Reliability
Durability is a cornerstone of engineering excellence. Whether it’s a hydraulic piston in a press or a connecting rod in an engine, longevity depends largely on what lies beneath the surface. Items crafted from poorly made base metal tend to suffer from fatigue much sooner than those forged from reliable sources.
This premature degradation can be traced back to factors such as low tensile strength, microstructural instability, and poor heat treatment response. Over time, microscopic cracks propagate faster, and corrosion sets in more readily. In hostile environments—such as marine, high-pressure, or high-temperature settings—the lack of resilience becomes even more pronounced.
Consequently, the costs of replacement, labor downtime, and customer dissatisfaction become recurring issues. In mission-critical sectors like energy infrastructure, offshore drilling, or aerospace, these risks are magnified. A component failure not only brings equipment offline but may also endanger lives and destroy brand credibility.
Moreover, reputational harm from warranty claims or product recalls often outpaces the initial savings gained from using cheap material. Engineers must always consider life-cycle performance, not just acquisition cost, when specifying raw inputs for load-bearing parts.
NO 4. Hidden Costs and Financial Losses
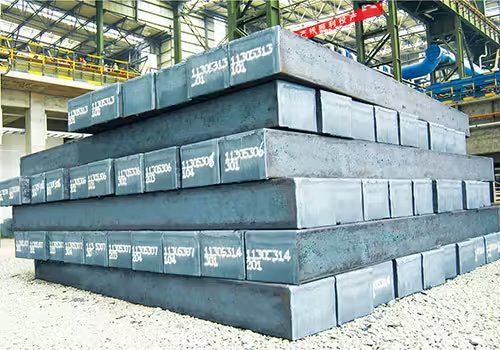
Opting for a low-cost billet of steel might seem financially beneficial at first. However, hidden costs quickly At first glance, lower-grade stock material might appear to offer cost advantages. After all, it often comes at a significantly reduced upfront price. However, this perceived savings quickly dissolves when the hidden operational expenses begin to surface.
These include elevated rejection rates during inspection, higher tool consumption during processing, and prolonged machining times due to inconsistent hardness or surface roughness. In some cases, the added need for secondary processes—like normalizing or stress relief—to correct flaws negates any initial savings.
To illustrate this point clearly, consider the following comparison:
Cost Factor | High-Quality Steel Input | Substandard Input |
---|---|---|
Scrap Rate | 2–5% | 15–25% |
Tool Maintenance Frequency | Monthly | Weekly |
Machining Time per Unit | Predictable | Inconsistent |
Quality Control Labor Hours | Minimal | Extensive |
Warranty Claims | Rare | Frequent |
Lifetime Cost per Component | Lower overall | Substantially higher |
As the table shows, the cost of poor decisions at the material sourcing stage scales rapidly as production ramps up. What appears economical on the balance sheet often becomes burdensome when viewed through the lens of productivity, risk mitigation, and product integrity.
NO 5. Safety Risks in Critical Applications
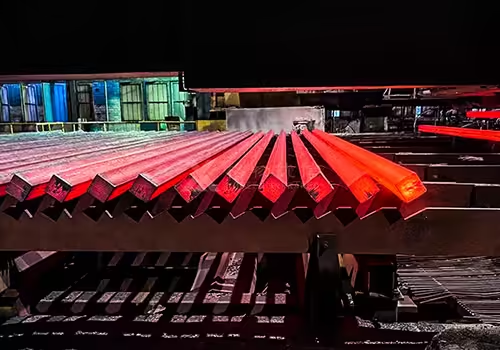
Safety in engineering and construction begins long before the assembly line—it starts with the selection of suitable raw inputs. When core materials used to manufacture structural parts are subpar, the consequences can be catastrophic.
Consider load-bearing applications in bridges, cranes, or heavy-duty vehicles. A defective section of forged steel can shear off under pressure, potentially causing fatal accidents. In pressure vessels or hydraulic systems, material failure could lead to explosions or toxic leaks. These outcomes aren’t just hazardous—they’re legally and ethically unacceptable.
In addition, many industries are governed by strict regulatory frameworks that mandate minimum mechanical performance criteria. Substances that do not meet these specifications will not pass inspections, certifications, or third-party audits. This can delay product rollouts, increase liability insurance premiums, or trigger legal penalties.
To ensure compliance and reduce safety risks, it is vital to source from providers who follow rigorous melt practices, maintain traceability, and adhere to recognized metallurgical standards. Comprehensive documentation—such as mill test reports (MTRs), certificates of conformance (CoCs), and third-party testing records—can help verify quality before integration into safety-critical systems.
Even for non-life-threatening applications, the risk of product failure can lead to lawsuits, environmental damage, or complete project halts. Simply put: cutting corners at the raw material stage endangers more than just the equipment—it puts people, businesses, and communities at risk.
Conclusion
Every manufacturer and engineer should prioritize material quality from the outset. The billet of steel forms the backbone of many industrial applications. Opting for a bad billet may save costs upfront but introduces numerous challenges and risks that outweigh the initial savings.
From structural failures and manufacturing defects to hidden costs and safety hazards, the reasons to avoid substandard billets are clear. By selecting the right billet of steel—tested, certified, and sourced responsibly—you ensure the longevity, safety, and efficiency of your products.
Take the time to vet your suppliers, request certifications, and implement quality control procedures. The integrity of your final product begins with the billet.
FAQ
What is a billet of steel used for?
A billet of steel is used as a raw material in the production of various metal products such as rods, bars, wires, machine parts, and structural components. It is a key intermediate product in steel processing.
How can you identify a bad billet of steel?
Visual inspections might not always reveal defects, so non-destructive testing, chemical analysis, and metallurgical evaluation are often necessary to assess the quality of a billet of steel.
Are all billets made using the same process?
No. Billets can be made through continuous casting or rolled from ingots. The quality may vary depending on the source, composition, and manufacturing controls.
What are the standards for a good billet of steel?
Standards vary by industry, but a good billet generally adheres to strict chemical composition, physical properties, and tolerance requirements as defined by organizations such as ASTM, ISO, or DIN.
Why is billet quality so important?
Because it directly affects the strength, durability, and safety of the final product. A poor-quality billet of steel can compromise everything from manufacturing efficiency to end-user safety.