
How 4140 Yield Stress Outperforms Others
Table of Contents
Introduction
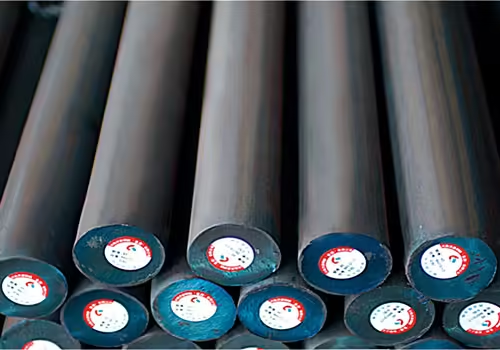
The 4140 yield stress is one of the most critical material properties when evaluating the performance and strength of alloys, particularly in industries like aerospace, automotive, and manufacturing. Known for its exceptional durability and high tensile strength, 4140 steel is commonly used for heavy-duty applications that require robust materials. Understanding how 4140 yield stress outperforms other materials helps manufacturers make better choices for specific projects. In this blog post, we will explore why 4140 yield stress is highly regarded in engineering and industrial fields, how it compares to other materials, and what advantages it provides for various applications.
What is 4140 Yield Stress?
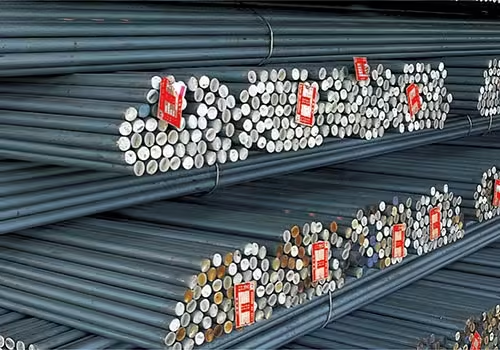
Before diving into its superior qualities, it’s essential to understand what 4140 yield stress refers to. Yield stress is the amount of stress a material can withstand without undergoing permanent deformation. In simpler terms, it is the point at which a material begins to experience permanent changes in its shape under applied force, such as bending, stretching, or compressing. The 4140 steel alloy, which consists primarily of chromium, molybdenum, and carbon, has an impressive yield stress that makes it highly sought after for applications requiring both strength and toughness.
The 4140 steel is often regarded for its excellent mechanical properties, and its yield stress is one of its most vital characteristics. The ability of this material to maintain its structural integrity under intense mechanical forces is what sets it apart from many other steel alloys. Whether it’s used in construction equipment, automotive parts, or aerospace components, the yield stress of 4140 ensures that these materials remain functional and safe under stress conditions where other materials may fail. The high yield stress contributes to its ability to retain its shape, making it a go-to choice for industries that rely on durable and long-lasting materials.
This unique combination of strength and toughness makes 4140 yield stress particularly valuable for components such as gears, shafts, crankshafts, and heavy-duty machinery. These applications demand both high strength to resist deformation and toughness to withstand impact and cyclic loading. The 4140 alloy’s ability to resist plastic deformation allows it to handle demanding work environments, which is a key factor in its widespread use in industries ranging from manufacturing to automotive and aerospace.
Why 4140 Yield Stress Outperforms Other Materials
4140 yield stress is not just about resistance to deformation—it also reflects how well the material performs under extreme conditions. This capability to endure stress while maintaining integrity makes 4140 steel ideal for tough applications, outshining other materials in the following areas:
Superior Strength-to-Weight Ratio
One of the standout features of 4140 steel is its superior strength-to-weight ratio. This means that 4140 can handle a significant amount of stress without adding unnecessary weight, which is especially important in industries like aerospace, automotive, and heavy machinery. In applications where weight reduction is a critical design goal, yet high strength is still required, 4140 steel is the material of choice. For example, in aerospace, components such as aircraft frames and landing gear require materials that offer the strength to withstand high forces without adding excessive weight, and 4140 steel excels in this regard. Similarly, in automotive engineering, parts like axles, gears, and suspension components can be manufactured using 4140 steel to ensure both performance and safety.
The material’s strength-to-weight ratio means that 4140 steel components can endure the forces placed on them over time without increasing the weight of the vehicle or machinery. By maintaining its strength while keeping weight low, 4140 allows for improved fuel efficiency and enhanced performance in a wide range of applications.
Increased Durability Under Pressure
Another defining feature of 4140 yield stress is its remarkable durability under high-pressure conditions. The refined microstructure of 4140 steel allows it to maintain its hardness and yield strength, even under extreme loads and mechanical stresses. This characteristic is vital for parts that undergo constant pressure, such as hydraulic systems, pressurized vessels, and engine components. 4140’s ability to resist wear and retain strength even under pressure makes it superior to other common materials like mild steel and stainless steel, which may fail under similar conditions.
Due to the combination of high yield stress and excellent fatigue resistance, 4140 can withstand the repeated stress cycles that many components face without experiencing permanent deformation. This quality is invaluable in industries that rely on components with long service life and minimal maintenance. For example, automotive manufacturers often choose 4140 for suspension parts, where the components are repeatedly stressed and loaded over time.
Resistance to Wear and Corrosion
Another area where 4140 steel outperforms other materials is in its resistance to wear and corrosion. While other materials may lose their functionality due to the wear of moving parts or exposure to corrosive substances, 4140 steel, especially when heat-treated, maintains its integrity for extended periods. The heat treatment processes, such as quenching and tempering, enhance its hardness and create a protective layer that significantly reduces wear and corrosion.
4140 steel’s ability to resist wear makes it a perfect choice for parts that are subjected to continuous friction, such as gears, axles, and shafts. Additionally, its corrosion resistance allows it to function in environments that would typically degrade other materials. This includes exposure to harsh chemicals, extreme temperatures, or even outdoor conditions, which can corrode unprotected metals. In industries like oil and gas or marine engineering, where components are constantly exposed to harsh conditions, 4140’s corrosion resistance is a key reason for its continued use.
Versatility in Heat Treatment
Another key factor that makes 4140 yield stress stand out is its versatility in heat treatment. Heat treatments such as quenching and tempering can be used to alter the material’s properties to suit specific applications. These heat treatments enhance the hardness, strength, and toughness of 4140 steel, providing manufacturers with a high degree of flexibility when tailoring the material to meet the demands of particular tasks.
The ability to adjust the heat treatment process allows 4140 to perform across a broad range of applications. For example, if a particular part requires more hardness to resist wear, a specific quenching process can be employed. If toughness is a priority, tempering may be used to ensure the material’s resistance to cracking under stress. This versatility in heat treatment allows manufacturers to customize the yield stress properties of 4140 to suit each application, making it an invaluable material in the manufacturing process.
By offering enhanced hardness and strength when needed, while maintaining the necessary toughness for certain applications, 4140 can be customized to meet the specific needs of industries such as automotive, aerospace, heavy machinery, and manufacturing.
Comparing 4140 Yield Stress with Other Materials
When comparing the 4140 yield stress with other commonly used materials, it becomes clear why it is a superior choice for many industrial and engineering applications. Here’s a breakdown of how 4140 compares to several other popular materials.
Material | Yield Stress (MPa) | Strength-to-Weight Ratio | Durability | Corrosion Resistance |
---|---|---|---|---|
4140 Steel | 655–850 | High | Very High | Good (with heat treatment) |
Mild Steel | 250–450 | Moderate | Moderate | Moderate |
Stainless Steel | 250–550 | Moderate | High | Very High |
Tool Steel | 600–1000 | High | Very High | Moderate to Good |
Note: Values are approximations and can vary depending on specific alloy compositions and heat treatment processes.
As the table shows, 4140 steel has a significantly higher yield stress than mild steel and stainless steel, making it more capable of withstanding extreme loads without deforming. While stainless steel may offer better corrosion resistance, 4140 steel excels in applications where both strength and durability under stress are paramount.
Applications of 4140 Yield Stress
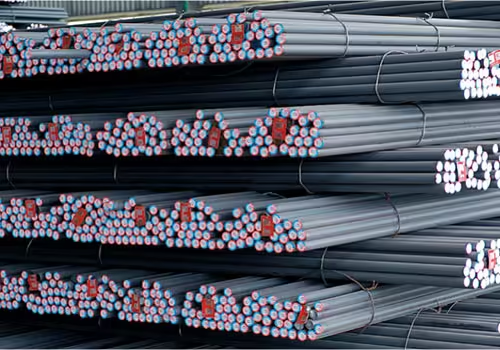
The high yield stress of 4140 steel makes it the preferred choice for several high-performance applications across various industries. Some of the most common uses of 4140 steel include:
- Automotive Components: 4140 is often used in the manufacturing of parts that require high tensile strength, such as axles, gears, and crankshafts.
- Aerospace: Lightweight and highly durable, 4140 steel is used for components like landing gear, turbine blades, and structural parts of aircraft.
- Heavy Machinery: The ability to withstand high stress makes 4140 ideal for parts like shafts, couplings, and gears used in heavy equipment.
- Oil and Gas: 4140 steel is utilized in drilling rigs, valves, and other parts that need to endure extreme temperatures and pressures.
How to Enhance 4140 Yield Stress
While 4140 steel already has remarkable yield stress, its performance can be further enhanced through several methods:
- Quenching: This heat treatment method involves heating the steel to a high temperature and then cooling it rapidly. This process increases the hardness and strength of the material.
- Tempering: After quenching, tempering can be done to relieve stress and improve toughness. This treatment is vital to achieving a balance between hardness and flexibility.
- Cold Working: Cold working processes like forging and rolling can further increase the yield stress of 4140 steel by refining its grain structure.
By carefully selecting the right combination of heat treatments and manufacturing processes, manufacturers can tailor 4140 steel to meet the specific demands of each application.
Conclusion
4140 yield stress is a defining characteristic of this steel alloy that makes it an ideal choice for high-performance applications. Its superior strength, durability, and resistance to wear and corrosion set it apart from other materials. Whether used in automotive components, aerospace, or heavy machinery, 4140 steel’s exceptional ability to withstand high stress without permanent deformation ensures its continued popularity across a wide range of industries.
With proper heat treatment and maintenance, 4140 steel can outperform other materials in even the most demanding environments. Understanding its potential and leveraging its properties allows manufacturers to create durable, efficient products that will perform reliably for years to come.
FAQ
What is the yield stress of 4140 steel?
The yield stress of 4140 steel typically ranges from 655 to 850 MPa, depending on the specific alloy composition and heat treatment.
Can 4140 yield stress be increased?
Yes, 4140 yield stress can be increased through heat treatments like quenching, tempering, and cold working.
Why is 4140 steel used in aerospace applications?
4140 steel is used in aerospace because of its high yield stress, strength-to-weight ratio, and resistance to wear and corrosion, making it ideal for structural components that must withstand high stress.
What industries benefit from 4140 steel?
4140 steel is widely used in automotive, aerospace, heavy machinery, and oil and gas industries for parts that require high strength and durability.
How does 4140 yield stress compare to other materials?
Compared to mild steel and stainless steel, 4140 steel has a significantly higher yield stress, which allows it to withstand more substantial forces without permanent deformation.