
4130 vs 4140: The Ultimate Showdown
Table of Contents
Introduction
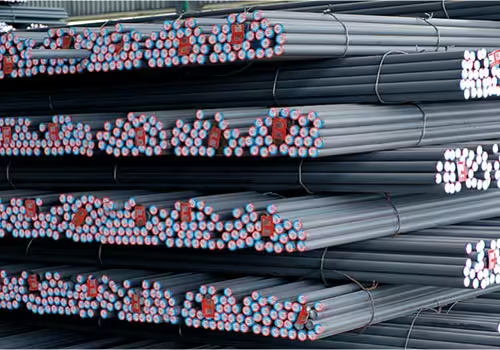
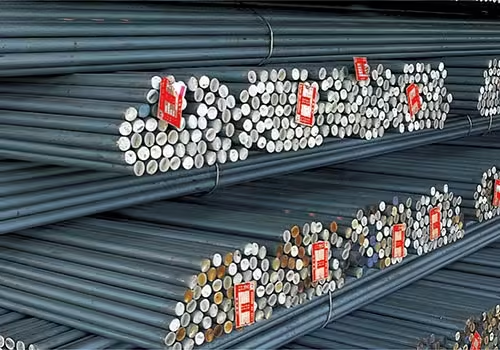
When it comes to choosing the right alloy steel for engineering, construction, or manufacturing applications, the debate between 4130 vs 4140 often comes up. These two chromium-molybdenum steels are closely related in composition and mechanical performance but have critical differences that can impact your project. Whether you’re building aerospace parts, automotive components, or structural equipment, selecting the correct steel grade is crucial. This blog dives deep into the differences, similarities, and ideal use cases for 4130 vs 4140 so you can make an informed decision.
Chemical Composition: Comparing the Core Elements of 4130 vs 4140
The chemical makeup of alloy steel plays a crucial role in determining its mechanical behavior, suitability for various applications, and how it responds to heat treatment and fabrication. In the case of 4130 vs 4140, both materials fall under the category of chromium-molybdenum (chromoly) low-alloy steels. Their compositions share many similarities, yet the subtle differences between them significantly influence their end-use performance.
Both 4130 and 4140 contain essential alloying elements like chromium and molybdenum, which improve hardenability, corrosion resistance, and overall strength. However, the key distinction lies in their carbon content, which directly affects hardness, strength, and machinability.
Key Composition Differences
- 4130 Steel: Contains approximately 0.28% to 0.33% carbon
- 4140 Steel: Contains approximately 0.38% to 0.43% carbon
This 0.10% increase in carbon content in 4140 steel makes it noticeably stronger and harder than 4130. That extra carbon enhances its tensile strength and wear resistance, making 4140 more appropriate for high-stress or heavy-load components like gears, axles, and shafts. However, with higher carbon also comes reduced weldability and increased difficulty in machining.
On the other hand, 4130’s slightly lower carbon content results in greater ductility and better weldability. This makes 4130 ideal for applications where parts need to be bent, formed, or welded—such as in aerospace tubing, bicycle frames, or custom vehicle fabrication.
When comparing 4130 vs 4140 based on chemical composition alone, the decision often hinges on the balance between strength and processability. If your project involves high-strength parts that undergo heavy stress, 4140 is generally the better fit. For projects requiring ease of welding and shaping, 4130 offers greater flexibility without sacrificing too much performance.
Mechanical Properties: Strength and Flexibility in 4130 vs 4140
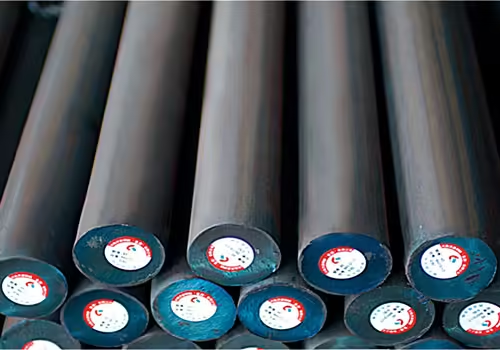
Understanding how 4130 vs 4140 perform under mechanical stress is vital. Engineers and designers must consider tensile strength, yield strength, elongation, and impact resistance when choosing between the two.
Mechanical Property Comparison
Property | 4130 Steel | 4140 Steel |
---|---|---|
Tensile Strength | ~97,000 psi | ~95,000 – 150,000 psi |
Yield Strength | ~63,000 psi | ~60,000 – 130,000 psi |
Elongation (%) | ~25 | ~20 |
Hardness (HB) | ~197 | ~217 |
Machinability | Good | Moderate |
Weldability | Excellent | Good |
As the table shows, 4140 steel excels in high-strength applications where wear resistance and load-bearing capability are priorities. However, 4130 provides better formability and is easier to machine, especially in its annealed state.
Applications: Choosing Between 4130 vs 4140 in Real-World Projects
Selecting between 4130 vs 4140 isn’t just about technical specifications; it’s about aligning the material properties with real-world functional requirements. These two alloy steels are widely used across industries because they offer specific benefits tailored to distinct applications.
Engineers typically analyze factors like tensile strength, yield, ductility, weldability, and resistance to wear before choosing between 4130 vs 4140. Understanding where each alloy excels helps ensure optimal material performance, cost efficiency, and long-term reliability in various operational environments.
Where 4130 Excels
4130 alloy steel offers an ideal balance of moderate strength, high toughness, and excellent weldability. Its lower carbon content compared to 4140 makes it more suitable for welding and forming operations.
Applications that benefit from 4130 include:
- Aerospace tubing and structural frames: 4130 is lightweight and offers solid strength-to-weight performance, making it suitable for airframes and critical aerospace support elements where ease of fabrication is essential.
- Automotive roll cages and structural bars: High impact resistance and ductility make 4130 a common choice in motorsports, particularly for roll cages where energy absorption and crash resilience are necessary.
- Bicycle frames: Many high-end performance and custom bicycles use 4130 because of its resistance to fatigue and its ability to be welded or brazed without distortion.
- Race car chassis and tubular frames: The steel’s combination of strength and flexibility allows for dynamic structural performance in high-speed vehicles.
In all of these applications, the deciding factor for choosing 4130 over 4140 often comes down to its machinability, ease of fabrication, and ability to handle moderate mechanical stress while remaining cost-effective.
Where 4140 Shines
4140 steel, with its higher carbon and chromium content, delivers greater hardness, tensile strength, and wear resistance. It performs better in high-load and high-friction environments, though it requires more careful handling during fabrication due to its lower weldability.
Common applications for 4140 include:
- Gears, axles, and drive shafts: The enhanced surface hardness and strength of 4140 make it ideal for rotating components that endure torque, friction, and stress over prolonged periods.
- Tooling and industrial dies: Applications requiring precision and resistance to wear benefit from 4140’s superior hardness after heat treatment.
- Heavy machinery and mining equipment: 4140 can withstand repetitive stress and extreme loads, making it perfect for parts like hydraulic components, track pins, and lift arms.
- Oil and gas components: The alloy’s ability to handle high-pressure environments without failure makes it suitable for downhole tools, valve parts, and pump shafts.
Choosing between 4130 vs 4140 in these settings hinges on performance needs. Where strength and abrasion resistance are non-negotiable, 4140 delivers consistent results.
Heat Treatment and Weldability: How 4130 vs 4140 Behave Under Processing
The processing behavior of 4130 vs 4140 differs mainly in their responses to heat treatment and welding. While both are capable of being hardened and tempered, their distinct chemical compositions affect their workability during fabrication.
Heat Treatment Response
- 4130: Suitable for quenching and tempering. It reaches moderate hardness levels while retaining good ductility. It’s generally easier to process and doesn’t require intensive heat treatment protocols unless specific strength targets are needed.
- 4140: Highly responsive to heat treatment and capable of achieving greater hardness and tensile strength than 4130. However, it is more sensitive to rapid cooling and may require precise controls to avoid brittleness or cracking.
Weldability
In terms of weldability, 4130 has a clear advantage over 4140. Its lower carbon content reduces the risk of cracking during welding and allows for easier post-weld machining or forming. 4140, on the other hand, demands preheating and post-weld heat treatment to mitigate the chances of cracking and to preserve mechanical integrity.
For fabricators, choosing 4130 vs 4140 may come down to how much welding and shaping is required in the production process.
Cost Efficiency and Availability of 4130 vs 4140
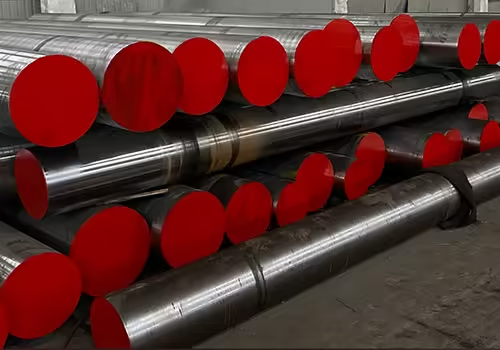
Beyond performance, material selection often involves budget considerations and supply chain factors. Both Beyond performance, material selection often involves budget considerations and supply chain factors. Both 4130 and 4140 are commercially available in a wide range of forms, but their pricing and processing costs vary.
Feature | 4130 | 4140 |
---|---|---|
Raw Material Cost | Lower | Moderate to High |
Heat Treatment Requirements | Moderate (optional for some uses) | High (essential for most applications) |
Machinability | Easier | Slightly more difficult |
Weldability | Excellent | Fair (requires pre/post-heat treatment) |
Availability | High in most standard sizes | High in industrial-grade formats |
From a cost perspective, 4130 tends to be more budget-friendly, especially when welding, machining, and forming are core parts of the manufacturing process. Its ease of use can reduce labor and equipment wear, leading to lower production costs.
On the other hand, if the job requires extended durability under high stress or load-bearing applications, the additional cost of 4140 may be justifiable. Choosing wisely between 4130 vs 4140 helps balance performance goals with financial efficiency.
Conclusion
In the debate of 4130 vs 4140, both steel grades offer distinct advantages depending on the application. 4130 is ideal for projects requiring high weldability and lower cost, while 4140 excels in strength and wear resistance for more demanding environments. Understanding the specific needs of your project will help you make the best choice between these two versatile steel types.
FAQ
What is the main difference between 4130 and 4140 steel?
The primary difference lies in carbon content—4130 has about 0.30%, while 4140 has around 0.40%. This affects strength, hardness, and weldability.
Is 4140 stronger than 4130?
Yes, due to the higher carbon content, 4140 typically has higher tensile and yield strength, making it better for high-load applications.
Can 4130 be welded more easily than 4140?
Absolutely. 4130’s lower carbon content makes it more weld-friendly. 4140 needs careful preheating and post-weld heat treatment to avoid cracking.
Which steel is better for machining?
4130 is generally easier to machine, especially in its annealed form. 4140 is machinable but often requires more advanced tooling and preparation.
Are both 4130 and 4140 readily available?
Yes, both are commonly stocked by suppliers in various forms like bars, tubes, and sheets. Availability may depend on specific dimensions and treatments.