
5 Common Problems with 1020 Steel Tubing and How to Avoid
Table of Contents
Introduction
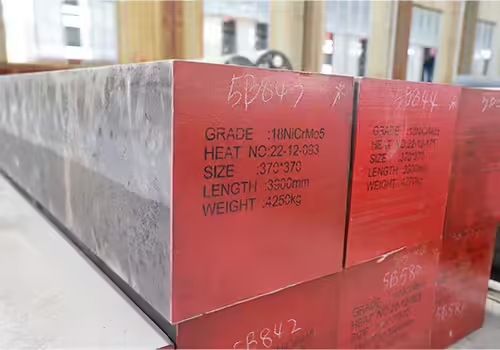
1020 steel tubing is widely used in various industries due to its excellent balance of strength, flexibility, and affordability. It is a popular choice for structural and mechanical applications, including automotive and manufacturing sectors. However, like all materials, it comes with its own set of challenges. Understanding these issues can help you maximize the performance of your 1020 steel tubing and avoid costly mistakes.
In this article, we will explore five common problems with 1020 steel tubing and offer practical advice on how to avoid them. Additionally, we will introduce Henan Jiyuan Iron & Steel (Group) Co., Ltd., a leading steel manufacturer that produces high-quality steel products, including 1020 steel tubing, and discuss how their advanced manufacturing processes can help resolve these challenges.
NO 1. Corrosion: A Major Issue for 1020 Steel Tubing
Corrosion is one of the most prevalent issues that affect 1020 steel tubing. Steel, including this particular grade, is highly susceptible to rust when exposed to moisture, salt, and certain chemicals. This is especially problematic in environments where the material is regularly subjected to outdoor or marine conditions. Over time, corrosion can severely weaken the steel, reducing its structural integrity, durability, and performance in critical applications.
How to Prevent Corrosion:
- Coatings and Galvanization: A highly effective method for protecting the tubing is to apply protective coatings, such as zinc galvanization. These coatings serve as a barrier between the steel and the corrosive elements in the environment. Zinc, in particular, is widely known for its ability to prevent rust formation and significantly extend the lifespan of steel products.
- Proper Storage: The environment in which steel is stored plays a critical role in preventing corrosion. It is essential to store the tubing in a dry and clean area that is shielded from direct exposure to moisture or any chemicals that may encourage rust formation. Avoid storing the material outside or in places with fluctuating humidity.
- Regular Maintenance: To ensure the continued integrity of your steel tubing, it is essential to conduct periodic inspections. These inspections should focus on early signs of corrosion, such as discoloration or surface rust. When these are detected early, preventive measures such as cleaning, re-coating, or replacing affected sections can be taken before further damage occurs.
NO 2. Deformation and Distortion During Fabrication
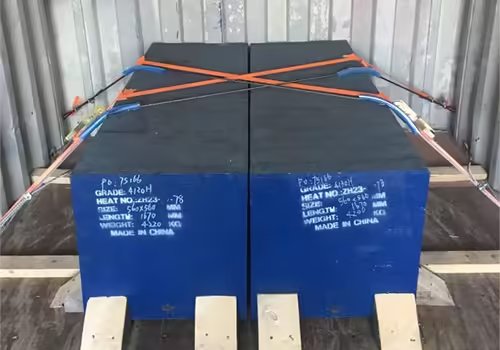
Deformation is another challenge when working with steel tubing. During fabrication processes such as bending or welding, the material can be subjected to high temperatures or mechanical stress. If not managed properly, these conditions can cause the tubing to warp or lose its original shape. This is especially problematic for applications where precision and exact dimensions are crucial.
How to Prevent Deformation:
- Proper Heating Techniques: When working with steel, uniform heating is key to preventing deformation. Whether you’re welding, bending, or forming the tubing, it’s important that the steel heats evenly to ensure consistent expansion and contraction. Avoid localized overheating, which can cause uneven stress on the material, leading to warping.
- Use of Jigs and Fixtures: Utilizing proper jigs, fixtures, and supports during the fabrication process can help maintain the correct dimensions of the material. These tools provide stability during bending or welding, helping to preserve the shape of the tubing and prevent deformation.
- Control Temperature and Speed: One of the most common causes of deformation during fabrication is uncontrolled heating or excessive speed during processes like welding. Maintaining a consistent and moderate speed during welding or other thermal treatments helps prevent stress build-up, ensuring that the material retains its shape.
NO 3. Welding Issues: Cracking and Weak Joints
Welding is a standard method for joining sections of steel tubing, but it introduces certain risks, including the possibility of cracks or weak joints. This can be a significant issue in high-stress applications where the welded sections are subjected to large forces. If the joints are not properly executed, the structural integrity of the entire assembly may be compromised.
How to Prevent Welding Issues:
- Proper Welding Techniques: To avoid the formation of cracks, it’s essential to use proper welding techniques, particularly for carbon steel. This includes preheating the steel before welding to reduce the temperature gradient between the weld and the surrounding material, as well as controlling the cooling process after welding. By managing these factors, you minimize the risk of stress cracking.
- Quality Filler Material: The choice of filler material is critical in ensuring the strength of the welded joints. Using high-quality filler that is compatible with the steel helps to form a strong bond that can withstand high stresses. Mismatched filler materials can result in weak joints that are prone to failure.
- Post-Welding Heat Treatment: After welding, it’s often beneficial to perform a post-weld heat treatment (PWHT). This process involves heating the welded area to a specific temperature and then gradually cooling it. PWHT helps to relieve the residual stresses created during welding, improving the overall strength and durability of the joint.
NO 4. Internal Defects and Inconsistencies in Steel Composition
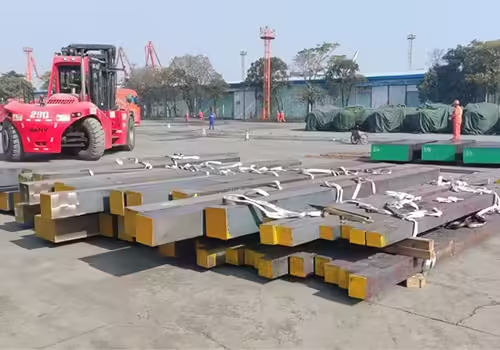
Internal defects and inconsistencies in the material’s composition can occur during the manufacturing process. These defects may not be visible on the surface, but they can significantly impact the material’s mechanical properties, such as strength, ductility, and overall performance. For applications requiring high reliability, these issues can lead to failures or reduced effectiveness.
How to Prevent Internal Defects:
- Quality Control During Production: The best way to avoid internal defects is to source steel from a reliable manufacturer with stringent quality control measures. Companies like Henan Jiyuan Iron & Steel (Group) Co., Ltd. use advanced technologies in their production processes to ensure that their steel products meet international standards and are free of defects that could compromise performance.
- Non-Destructive Testing: Non-destructive testing (NDT) methods, such as ultrasonic or X-ray inspection, are valuable tools for detecting internal defects in the steel. These methods allow for a thorough examination of the material without damaging it, ensuring that defects can be identified and addressed before the tubing is used in critical applications.
NO 5. Inadequate Strength for Heavy-Duty Applications
While 1020 steel tubing is known for its versatility, it is not always suitable for heavy-duty applications. Its strength may not be sufficient to withstand the high loads or extreme stresses encountered in certain industries, leading to potential failure under intense conditions.
How to Prevent Strength Issues:
- Material Selection: For applications that require higher strength, it is advisable to opt for a stronger grade of steel tubing. For example, 4140 steel tubing offers superior strength and fatigue resistance compared to 1020 steel, making it a better choice for heavy-duty applications.
- Reinforced Steel Tubing: If 1020 steel tubing is the preferred material, consider using reinforced designs that enhance load-bearing capabilities. By increasing the thickness of the tubing or utilizing reinforced construction, you can boost its strength without sacrificing flexibility, making it suitable for more demanding applications.
The Role of Henan Jiyuan Iron & Steel (Group) Co., Ltd. in Overcoming Common 1020 Steel Tubing Problems
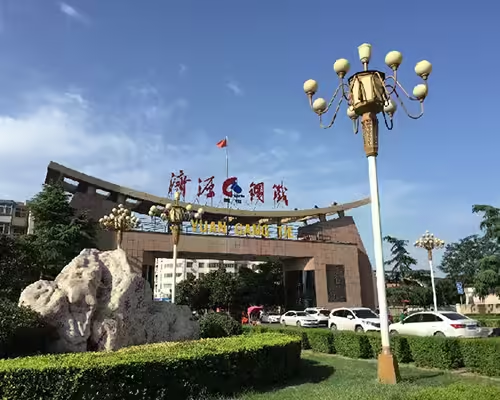
Henan Jiyuan Iron & Steel (Group) Co., Ltd., established in 1958, is a major steel manufacturer based in Jiyuan City, Henan Province. With over 8,000 employees and an annual production capacity of 5 million tons, the company is a leading producer of a wide range of steel products, including high-quality 1020 steel tubing.
Their advanced manufacturing processes and rigorous quality control standards ensure that the steel products are free from defects and meet international standards. This helps mitigate many of the common problems faced by users of 1020 steel tubing, such as corrosion, deformation, and welding issues.
Table: Comparison of Common 1020 Steel Tubing Problems and Solutions
Problem | Cause | Solution | Impact of Solution |
---|---|---|---|
Corrosion | Exposure to moisture and chemicals | Apply protective coatings and store properly | Extends tubing life and performance |
Deformation during fabrication | Uneven heating or mechanical stress | Use jigs and proper heating techniques | Maintains precision and prevents shape loss |
Welding Issues | Cracking or weak joints | Use proper welding techniques and quality filler material | Strong, durable joints for high-stress applications |
Internal Defects | Manufacturing inconsistencies | Implement quality control and NDT testing | Ensures uniform quality and reliability |
Inadequate Strength | Low strength for heavy-duty tasks | Select higher-grade tubing or reinforced designs | Ensures safety and performance under heavy loads |
Conclusion
1020 steel tubing is a versatile and cost-effective material widely used in many industries. However, it is not without its challenges. By understanding the common problems and implementing the solutions outlined in this article, you can avoid these issues and ensure that your 1020 steel tubing performs at its best. Always prioritize quality control and work with reputable manufacturers, like Henan Jiyuan Iron & Steel (Group) Co., Ltd., to ensure that you receive the highest quality steel products available.
FAQ
What are the main applications for 1020 steel tubing?
1020 steel tubing is commonly used in automotive, construction, and manufacturing industries, particularly in applications requiring moderate strength and flexibility.
How can I prevent corrosion on 1020 steel tubing?
You can prevent corrosion by applying protective coatings, storing the tubing in dry environments, and performing regular maintenance checks.
Can 1020 steel tubing be welded?
Yes, 1020 steel tubing can be welded, but it requires careful attention to welding techniques to prevent cracking and ensure strong joints.
What is the best way to handle deformation during fabrication?
To avoid deformation, ensure that the tubing is heated evenly and use jigs to maintain the correct shape during fabrication processes.
How does Henan Jiyuan Iron & Steel (Group) Co., Ltd. ensure the quality of its 1020 steel tubing?
Henan Jiyuan Iron & Steel (Group) Co., Ltd. employs advanced manufacturing technology, stringent quality control measures, and conducts thorough testing to ensure the high quality and reliability of its steel tubing.