
1020 Carbon Steel: 5 Buyer Pitfalls You Must Avoid
Table of Contents
Introduction
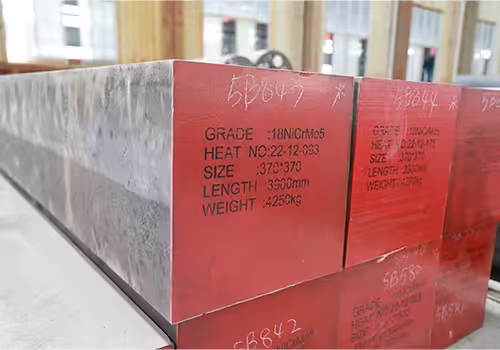
1020 carbon steel is a widely used low-carbon steel that features excellent weldability, moderate strength, and good machinability. Due to its balanced properties and relatively low cost, it finds use in various industries including automotive, construction, agriculture, and manufacturing. Despite its popularity, many buyers make critical mistakes when sourcing and utilizing this material.
Understanding these common pitfalls can save time, money, and operational inefficiencies. This article explores five significant pitfalls buyers often face when dealing with 1020 carbon steel. By identifying these issues, companies and procurement teams can make better-informed purchasing decisions and avoid costly missteps.
Pitfall 1: Misunderstanding 1020 Carbon Steel Specifications
One of the most frequent mistakes made by buyers is not fully understanding the specifications of 1020 carbon steel. While it has moderate strength and excellent weldability, its composition limits its use in applications that require higher toughness, hardness, or wear resistance.
Buyers should ensure that the 1020 carbon steel they are purchasing complies with the appropriate ASTM standards (such as ASTM A29 or ASTM A513) based on the material’s form and intended use. Variations in composition, heat treatment, or manufacturing processes can lead to inconsistencies in performance.
In addition, some suppliers may offer products that sound similar to 1020 carbon steel but are not true to the specification. Always request a Material Test Report (MTR) to confirm the material’s properties and ensure it is suited for the intended application.
Key Tip:
For example, 1020 carbon steel might be appropriate for applications like structural supports or shafts, but for more demanding applications such as gears or tools, higher-carbon steels like 1045 or 4140 might be necessary. Failing to understand these nuances can lead to costly mistakes and subpar performance.
Pitfall 2: Overlooking Heat Treatment Limitations
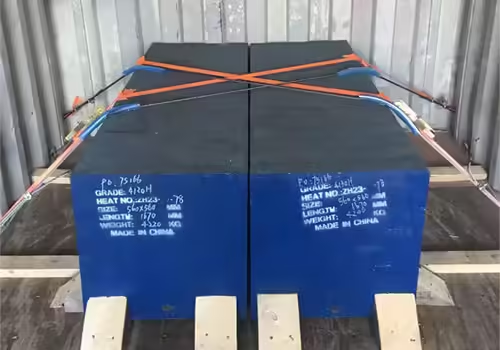
Another major pitfall when working with 1020 carbon steel is assuming that it can be heat-treated to achieve high levels of hardness or strength, similar to higher-carbon steels. However, 1020 carbon steel does not respond well to traditional heat treatment methods like quenching and tempering. This is primarily due to its low carbon content (approximately 0.20%), which limits its ability to undergo hardening processes that would typically increase its strength and hardness.
While 1020 carbon steel can be surface-hardened through methods like case hardening or carburizing, it is crucial to note that these processes only affect the surface layer, while the core remains relatively soft. This means that the material might be well-suited for applications where moderate surface hardness is sufficient, but it is not ideal for high-stress applications that require high overall strength or toughness throughout the entire material.
For instance, using 1020 carbon steel for tools, machinery parts, or components subject to high wear or impact could result in premature failure or insufficient durability. In such cases, higher-carbon steels such as 1045 or alloy steels like 4140 would be better choices due to their ability to harden through the entire thickness.
This limitation is important to consider, especially when selecting materials for parts that will endure continuous stress, high loads, or abrasion. When these conditions are not matched with the material’s capabilities, you could face a costly outcome of rework, replacement, or downtime.
Key Tip:
To maximize the performance of 1020 carbon steel, use it in applications where moderate strength and surface hardness are sufficient. Avoid using it for components that require uniform high strength or extreme wear resistance. For those applications, higher-carbon or alloy steels like 1045 or 4140 are better suited.
Pitfall 3: Ignoring Surface Finish Requirements
When purchasing 1020 carbon steel, many buyers overlook the importance of specifying the correct surface finish. This oversight can lead to various challenges, especially for components that will undergo machining, welding, or coating. The quality of the surface finish directly impacts the material’s workability, welding ease, and overall performance.
For example, 1020 carbon steel is available in multiple finishes, including hot-rolled, cold-drawn, and turned and polished versions. Hot-rolled 1020 carbon steel is generally less precise in terms of dimensions and surface smoothness, but it comes at a lower cost and is suitable for less critical applications. On the other hand, cold-drawn 1020 carbon steel provides superior dimensional accuracy and a smoother finish, but it comes at a higher price.
For applications requiring precise dimensions, better aesthetics, or a smoother surface, cold-drawn 1020 is the preferable choice. This is particularly relevant for parts that need to fit within tight tolerances or undergo post-processing, such as machining or painting. A poor surface finish can cause defects during these processes, reducing tool life, increasing the likelihood of rework, and raising the cost of production.
Moreover, the surface finish can significantly impact the material’s behavior during welding. Hot-rolled steel often requires additional cleaning, grinding, or preparation to ensure a good bond during welding, which adds to labor costs and time. A smooth, cold-drawn finish, in contrast, is much easier to work with and reduces these additional steps.
Surface imperfections can also affect post-manufacturing processes such as coating or painting. Poor surface quality can result in weak adhesion, which may lead to peeling, corrosion, or reduced durability of the final product. These extra costs can be easily avoided by choosing the correct surface finish early in the procurement process.
Key Tip:
When purchasing 1020 carbon steel for applications requiring precision or aesthetic appeal, opt for cold-drawn steel for better surface quality. If surface finish is less critical, hot-rolled material may be sufficient. Always communicate your surface finish requirements clearly to the supplier to avoid costly rework.
Pitfall 4: Failing to Consider Form and Size Availability
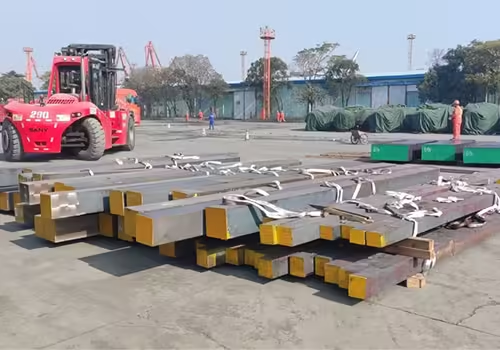
Another frequent oversight is neglecting to check the availability of the required form and size of 1020 carbon steel. It is commonly available in bar, tube, and sheet forms, but not all sizes are readily stocked.
Custom orders or rare dimensions can lead to longer lead times and higher costs. Collaborating with suppliers to confirm inventory and production capabilities can save significant time. Below is a table showing typical forms and size ranges for 1020 carbon steel:
Form | Typical Size Range | Common Use Cases |
---|---|---|
Round Bar | 1/4 inch to 12 inches | Shafts, pins, machine parts |
Square Bar | 1/2 inch to 4 inches | Frames, supports, brackets |
Tubing | OD 1/2 inch to 4 inches, wall 0.065″+ | Hydraulic lines, structural applications |
Sheet/Plate | Thickness 0.035″ to 2 inches | Panels, guards, chassis components |
Understanding availability can help optimize design decisions and reduce sourcing challenges. Larger bulk orders may require additional lead time, while some suppliers might not carry certain profiles in-house.
Key Tip:
Plan ahead by confirming dimensions and availability early in the design phase to avoid delays in your production schedule.
Pitfall 5: Neglecting Supply Chain and Certification Factors
One of the most critical aspects of purchasing 1020 carbon steel is ensuring that the material comes from a reliable and certified supplier. Many buyers fail to fully vet the supply chain and certifications of their steel supplier, which can lead to a range of problems, from receiving substandard or mislabeled materials to facing issues with quality control and regulatory compliance.
Without the proper documentation, including mill certificates, traceability reports, and compliance with industry standards, there is a risk of receiving materials that do not meet the required specifications. Additionally, some suppliers may not have strict quality control measures in place, leading to inconsistencies in the materials they deliver.
In industries that have stringent quality requirements—such as automotive, aerospace, and manufacturing—certification is critical. Without proper documentation to verify the material’s composition and quality, you risk failing to meet industry regulations, which could result in penalties, recalls, or reputational damage.
Moreover, the global supply chain for steel is complex, and material shortages or disruptions can impact delivery schedules. Working with reputable and transparent suppliers who can provide full traceability and relevant certifications (e.g., ISO, ASTM) helps mitigate these risks. Reliable suppliers ensure that the material arrives on time and meets quality standards.
Key Tip:
Work with suppliers who are willing to provide full traceability and relevant compliance certifications to ensure the material meets quality standards and complies with industry regulations. This will protect your production processes and mitigate the risk of defects or non-compliance.
Conclusion
1020 carbon steel remains a versatile and affordable material, but buyers must navigate several critical pitfalls to ensure it meets performance and quality expectations. From understanding specifications and heat treatment limitations to surface finish, size availability, and supply chain integrity, each factor plays a vital role in a successful purchase.
Avoiding these common mistakes leads to better product performance, fewer returns, and smoother operations. Taking a proactive approach in evaluating and sourcing 1020 carbon steel ultimately benefits the bottom line and enhances project outcomes.
When you treat your material sourcing process with the same precision as your engineering, you gain a competitive edge. Let your purchase decisions reflect both strategic insight and technical understanding.
FAQ
What are the main uses of 1020 carbon steel?
1020 carbon steel is used for applications requiring moderate strength and good weldability, including automotive parts, machinery components, and structural elements.
Can 1020 carbon steel be hardened?
It can be surface-hardened using case hardening techniques, but it does not respond well to full quenching and tempering due to its low carbon content.
Is 1020 carbon steel good for welding?
Yes, it has excellent weldability, making it a preferred choice in fabrication and structural projects.
How does 1020 carbon steel compare to 1045?
While both are carbon steels, 1045 has a higher carbon content, offering better hardness and strength but lower weldability and machinability.
What should I check when buying 1020 carbon steel?
Always verify the material test report, surface finish, size availability, and supplier certifications to ensure you receive authentic and suitable material.
Does 1020 carbon steel rust?
Like other carbon steels, 1020 is prone to rusting if left unprotected. Protective coatings or paint can help extend its service life in corrosive environments.
Can I use 1020 carbon steel in outdoor applications?
It can be used outdoors if adequately coated or galvanized, but untreated steel may corrode over time when exposed to the elements.
What machining techniques work best on 1020 carbon steel?
Standard turning, milling, and drilling operations work well. Carbide tools and proper coolant flow improve surface finish and tool longevity.
Is 1020 carbon steel environmentally friendly?
While not as sustainable as recycled or stainless steel, 1020 carbon steel is widely recyclable and can be reused in various manufacturing processes.
Can I substitute 1020 carbon steel with other materials?
Yes, depending on application needs. Alternatives like 1045, 4140, or stainless steel may offer better performance in strength, corrosion resistance, or wear.